Centre for Engineered Coatings (CEC)
Solution Precursor Plasma Spray (SPPS) Technology
Overview
SPPS is an exciting method to produce a wide variety of functional oxide ceramic coatings, starting with appropriate solution precursors in contrast to powder feedstock in case of conventional plasma spraying. The technique utilizes aqueous/organic chemical precursor solutions fed into the high temperature plasma plume through a dedicated delivery device. The solvent vaporizes as the droplet travel downstream to form solid particles, and are heated & accelerated to the substrate to form finely structured coating deposits.
Key Features
The SPPS process opens up new avenues for developing compositionally complex functional oxide coatings, with the following benefits:- ability to create nanosized microstructures without any feeding problems normally associated with powder-based systems,
- flexible, rapid exploration of novel precursor compositions and their combinations
- circumvention of expensive powder feedstock preparation steps,
- better control over the chemistry of the deposit
Potential Applications
- YSZ based TBCs for gas/steam turbine applications
- Pure ï¡-Al2O3 based dielectric coatings
- Graphene films for wear resistance, energy storage applications
- LSM, LiFePO4, etc for electrodes (anode & cathode) of SOFCs/Li-Ion Batteries
- Ferrites and Titania for photocatalytic applications
- Solar absorption coatings
Intellectual Property Development Indices (IPDI) 
- Developed wide ranging functional coatings for diverse industrial applications
- Prototype demonstration of various coatings is in progress
Status | 1 | 2 | 3 | 4 | 5 | 6 | 7 | 8 | 9 | 10 |
Major Patents / Publications
Major Patents*
Major Publications
- Easwaramoorthi Ramasamy, Sivakumar Govindarajan, Shrikant Joshi, Production of Graphene based Materials by Thermal Spray, ARCI patent appln. no. 2626/DEL/2015
- G. Sivakumar, R.O. Dusane, and S.V. Joshi, “Understanding the Formation of Vertical cracks in Solution Precursor Plasma Sprayed Yttria-Stabilized-Zirconia Coatings”, Journal of American Ceramic Society, 97(11), 3396-3406, 2014
- G. Sivakumar, Rajiv O. Dusane and Shrikant V. Joshi, A novel approach to process phase pure ï¡-Al2O3 coatings by solution precursor plasma spraying’, Journal of the European Ceramic Society, 33 (2013) 2823–2829
Development of Complaint Glass Seals for High Temperature Applications
Overview
Joining of metals ceramic parts for high temperature application by complaint (using glue) is prime requirement in the field of solid oxide fuel cell (SOFC), oxygen sensors, thermocouples, high temperature thread lock etc., Development of such high temperature glue are in progress. Sodium silicate/alumina based glue are successfully developed for 800oC applications. The developed paste was demonstrated by using some of the in-house repair work. Further, successfully join silica and Invar-36 for 800oC application. Additionally silica, stainless and silicon carbide flange also demonstrated.
Key Features
- Sealant is in powder and liquid form.
- As per requirement, one can make past prior to application.
- Brush, spatula, or dispenser can do application.
- Low curing temperature in the order of 150oC.
Potential Applications
- Electrical such as heater and lamps.
- High temperature sodium batteries
- Sealant for solid oxide fuel cells
- Temperature probes bonding to the required surface.
- Refractory insulations.
Intellectual Property Development Indices (IPDI) 
- Feasibility studies on SS/SiC/SiO2 was done
- Repair on broken porcelain flange was done as in-house work
- Silica dome and Invar flange was successfully join for another government sector company.
Status | 1 | 2 | 3 | 4 | 5 | 6 | 7 | 8 | 9 | 10 |
High Power Impulse Magnetron Sputtering (HiPIMS) facility
Overview
Magnetron sputtering is one of the well-known Physical Vapor Deposition (PVD) technique for generating defect-free thin films at low deposition temperatures. Contrary to any other PVD techniques, magnetron sputtering is a process in which the removal of the target material (in other words like evaporation) takes place through the momentum transfer process. Since it is a momentum transfer process, literally using this technique, most of the materials deposition can be done. In similar lines, High Power Impulse Magnetron Sputtering (HiPIMS) is a process in which, the power given to the source/target will be in short pulses of very high energy. In general, the high energy ionic depositions are known for achieving good adhesion, high density and good control over reactive process. As on date, the HiPIMS facility at ARCI is a lab scale equipment with planar as well as cylindrical cathodes. The HiPIMS facility with its unique advantages can be used for developing thin films that are key to major sectors like, automobile, aerospace, manufacturing, optics, electronics, alternate energy, biomedical, sensors, etc.
Key Features
- The facility can be used to deposit any metallic or reactive depositions (Metals, Metal nitrides, metal oxides & metal carbides)
- Can be used to develop thin films on internal or external surfaces of any regular objects
Potential Applications
- Any metallic, nitride or oxide coatings can be deposited
- Solar selective coatings for solar thermal applications
- Diffusion barrier coatings for electronic components
- Decorative coatings for aesthetic applications
- Biocompatible coatings for biomedical applications
- Coatings for developing different sensors
Intellectual Property Development Indices (IPDI) 
Status | 1 | 2 | 3 | 4 | 5 | 6 | 7 | 8 | 9 | 10 |
Major Patents / Publications
Major Publications
- Patent: “Improved cylindrical magnetron cathode and a process for depositing thin films on surfaces using the said cathode” application No. 21/DEL/2008, January 3 2008.
Axial Suspension Plasma Spray (ASPS)
Overview
Specifications
- High energy plasma power upto 150 kW to spray wide ranging ceramics, cermets, alloys, metal powders and fine particle suspensions
- Plasma jets: up to three, converging mode using Argon, Nitrogen, Hydrogen
- Axial Feedstock injection along the plasma flow
- Dual feed Axial Plasma Spray Torch configured to spray powders and suspensions
- Six-axis Robotic handling
Details
High energy Axial Plasma spray technique is capable to spraying powders and fine particle suspensions. In comparison with conventional radially injected plasma spray systems, the axially injected powder particles attain better momentum and greater heat transfer while travelling along the plasma plume. Therefore, the axial plasma sprayed coatings exhibit good deposition rate and efficiency and also, offer possibilities of engineering the microstructure with dense, porous and cracked features.
Fine structured coatings provide improved properties than micron-sized coatings. However, the fludized powder feeding arrangement are incapable of injecting fine particles, which necessitates the use of liquid based feeding either as suspensions or solution precursor based spraying. Additional capabilities of axial plasma spraying can be realized through efficient spraying of fine particle suspensions which otherwise are difficult with radial injection systems. Axial suspension plasma spray (ASPS) is an emerging coating technology through the use of fine-sized powder particles suspended in a suitable solvent such as water or ethanol and injected into the plasma flame to get desired microstructure. Unique features of axial suspension plasma spray are,
- Tailored microstructure – dense, porous, columnar, vertically cracked, feathery
- High spray rate
- Relatively thin coatings are possible compared to conventional thermal spray
- Better surface finish
- Wide range of materials – cermets, ceramics, metals and alloys
Prominent application areas with axial plasma spray technique include industries requiring thermal barrier, dielectric, insulation, wear, corrosion resistance and refurbishment. For example, YSZ based thermal barrier coatings applied through ASPS exhibit lower thermal conductivity and identical microstructure similar to that EBPVD process, which can be effectively exploited for cost-effective thermal barrier coatings in gas turbine components.
Status | 1 | 2 | 3 | 4 | 5 | 6 | 7 | 8 | 9 | 10 |
Activated Combustion High Velocity Air-Fuel (HVAF)
Overview
Specifications
- Capable to generate 200 kW equivalent combustion power to spray wide ranging cermets, alloys and metal powders
- Convertible mode of spraying to deposit higher particle sized powders
- Internal geometry coating capability
- Specialized torch for spraying Carbide coatings and thin wear resistant coatings
- Six-axis Robotic handling
Details
Activated Combustion High-velocity Air-Fuel (HVAF) spray utilises compessed air and LPG fuel combination to generate high velocity gas streams. The optimized combination of high kinetic energy – ideal thermal input allows deposition of coatings with excellent microstructural features including fully dense, defect-free, retained phases and high adhesion strength. The exceptional capabilities can be understood from its highest productivity amongst the competing thermal spray techniques to reach as high as 35 kg/hr for Cr3C2-NiCr based coatings.
The process involves a pre-mixed Air-fuel mixture fed to the combustion chamber through the ceramic insert which is ignited initially with a spark plug. As the Combustion proceeds, the ceramic insert at the entrance of the combustion chamber gets heated up above the auto-ignition temperature of the mixture and takes the role of spark plug to enable stable combustion (also known as “Activated combustion”) throughout the process. The flame temperature during HVAF is much lower than that of HVOF since it uses an air-fuel mixture instead of an oxy-fuel mixture, which allows HVAF to coat thermally sensitive material with lesser thermal deterioration. Control of gas dynamics through the use of diverse nozzles results in range of particle velocities, which translates into highly adhesive, hard, oxide and pore-free coatings. Prominent application sectors with HVAF technique include industries requiring wear, corrosion resistance and refurbishment.
Status | 1 | 2 | 3 | 4 | 5 | 6 | 7 | 8 | 9 | 10 |
Slurry Coating Facility
Overview
The development of low cost coating for corrosion and environmentally sensitive metallic substrates are inevitable in high temperature application. One such low cost processing techniques is slurry coating. This coating process involves spray the formulated coating material applied to the area to be coated and heated in an ambient or under inert gas atmosphere. The major part of research and development activates involves preparation of suitable slurry.
Key Features
The slurry process make new opening for developing various metal ceramic and composites coating with following merits.
- Low cost
- Lack of access to machinery capable of other deposition methods
- Flexibility to apply the coating to complex surfaces
- Composites of metal-ceramic, polymer-ceramics, metal-polymers etc.,
Potential Applications
- Thermal protection shield for low melting substrates such as aluminum and polymer composites.
- Copper-glass composites for high temperature electronics.
- Slurry based environmental barrier coatings (EBC) on silicon carbide.
Intellectual Property Development Indices (IPDI) 
- Exploratory studies on aluminum and polymeric substrates for thermal protection.
- Copper thick printing on alumina and aluminum nitride.
Status | 1 | 2 | 3 | 4 | 5 | 6 | 7 | 8 | 9 | 10 |
Cathodic Arc Physical Vapor Deposition Facility (CAPVD)
Overview
In general, Cathodic Arc PVD is a three step process: (i) Vaporization of required material from a source (cathode) by using an electric arc, (ii) Transport of vaporized material to the destination (target to be coated) and (iii) Condensation of transported vapours on to the targeted object to make a thin film. The major advantages of the CAPVD include; formation of highly dense and adherent coatings with a good deposition rate and thickness control (± 5 nm). The semi industrial available facility at ARCI is associated with 400 mm length (Ф: 110 mm) cylindrical cathodes which enable reduced droplets formation than any other conventional CAPVD facilities. The maximum dimensions of the target to be coated can be: 350 mm L x 100 mm W (Ф). The CAPVD facility with its unique advantages can be used for developing thin films/ coatings in major sectors like; auto mobile, aerospace, manufacturing, optics, electronics, alternate energy, etc.
Key Features
- Films/coatings of different structures with good control over chemistry and thickness can be developed: (i). Mono-layer, (ii) Multi-layer, (iii) Gradient and (iv) Functionally multi-layered/graded
- Films/coatings containing Ti, Cr, AlSi & AlTi can be coated in pure metallic or nitride or carbide form. i.e. TiN, CrN, TiAlN, TiAlSiN, CrAlSiN, TiCrAlSiN, TiC, TiCN, TiAlCN, etc.
- Physical and mechanical properties can be tuned by varying deposition conditions
- Environmentally green and easily up scalable process with high production rates
Potential Applications
- Hard and wear resistant coatings for cutting tools – up to hardness of 45 GPa
- - High speed and dry machining
- - Machining of advanced materials: CGI, Ti6Al4V, Inconel 718, etc.
- Wear resistant coatings for dies, bearings, etc. – Low friction coefficient of < 0.2
- Erosion resistant coatings for compressor blades – A thickness of 20 μm is achieved
- Solar selective coatings for solar thermal applications – ~ α: 0.96 & ε: 0.09 at 400°C
- Diffusion barrier coatings for electronic components
- Decorative coatings for aesthetic applications, etc.
Intellectual Property Development Indices (IPDI) 
- Different nanocomposite hard coatings were developed and tested for their performance
- 20 μm thick TiCrN erosion resistant coating developed
- TiCrCN wear resistant coatings were demonstrated for die applications
- Cr/TiCrAlN/TiAlN/AlSiN/AlSiO solar selective coatings were demonstrated on 75 mm diameter SS tubes (~ α: 0.96 & ε: 0.09 at 400°C)
Status | 1 | 2 | 3 | 4 | 5 | 6 | 7 | 8 | 9 | 10 |
Major Patents / Publications
Major Publications
- “An improved solar selective multi-layer coating and a method of depositing the same” Application No. 1567/DEL/2012, May 22nd 2012.
- "Studies on cathodic arc PVD grown TiCrN based erosion resistant thin films" Krishna Valleti, Puneet C, Rama Krishna L, and Shrikant V. Joshi, JVST A 34, (2016): 041512
- “High temperature stable solar selective coatings by cathodic arc PVD for heat collecting elements” Krishna Valleti, D. Murali Krishna, P. Mohan Reddy, Shrikant V. Joshi, Solar Energy Materials and Solar Cells 145 (2016):447
Cold Gas Dynamic Spray Technology
Overview
Cold gas dynamic spray (also called Cold Spray or Kinetic Spray) involves accelerating micron sized powder particles to supersonic velocities resulting in the formation of dense, thick and pure coatings with high deposiotion rates. Cold spray is a low temperature high velocity variant of thermal spray family. This technique has very high deposition rates and deposition efficiencies. Since there is no heating of powders, retention of powder properties in the coating is possible. Dense coatings with porosity less than 0.1% can be achieved. Metallic, Alloy, Composites, Nanostructured and Amorphous powders can be deposited. This technology has huge potential for repair and refurbishment, electrical and thermal applications.
Key Features
- Indigenously developed state of the art PLC based automated Portable control panel (Max Pressure – 20 bar)
- Different set of nozzles
- For Low melting materials (polymer based)
- High deposition rate or coverage area
- Low deposition rate or coverage area
- For Ni based materials, Steels (Optional)
- Compressed AIR as process and carrier gas
- Maximum Pressure- 20 bar; Maximum Temperature-600oC
- Cu, Al, Ag, Zn, Sn,Ni, SS, Ta, Nb, Ti and alloys and composites
Potential Applications
- Repair and Refurbishment Applications ( Aerospace components such as Compressor Fan casing etc.,)
- Coatings for Electrical contacts, lugs, EMI shielding, heat sinks
- Coatings for High Temp Corrosion resistance, Bio medical, Sputter Target
- Sacrificial coatings or Cathodic Protection (Zinc coating on Steel Strcutures)
- Anodic Protection coatings (Aluminium coatings on Active Magnesium aerospace and automotive components)
- Wear resistant coatings ( MMCs, Alloy coatings)
- Nanostrcutured / amorpohous/ BMG coatings
- High Entropy Alloy Coatings as Bondcoats for High Temperature Gas Turbine Applications
Intellectual Property Development Indices (IPDI) 
- Technology Ready for Adaptation
- Application Development Activities in progress
Status | 1 | 2 | 3 | 4 | 5 | 6 | 7 | 8 | 9 | 10 |
Major Patents / Publications
Major Publications
- Naveen M Chavan, SP Phani, M Ramakrishna, DS Rao and G Sundararajan, Surface & Coatings Technology 205 (2011), P4798–4807
- G Sundararajan, Naveen M Chavan and S Kumar, Journal of Thermal Spray Technology, 1348—Volume 22(8) December 2013
- S Kumar, A.Jyothirmayi, Nitin Wasekar and SV Joshi, Surface and Coatings Technology, 296(2016), 124-135
Pulsed Electrodeposition Technology
Overview
Pulsed Electrodeposition is a unique non-line-of-sight electrolytic deposition technique for obtaining wear and corrosion resistant nanocrystalline coatings using modulated currents. The process utilizes non hazardous electrolyte and pulsed current to achieve desired microstructure and mechanical properties in hardness gradient nanocrystalline Nickel, Sacrificial Zn, Nanocrystalline alloys of Ni-P, Ni-W, Ni-Mo, Fe-W coatings. The technology is explored for grain boundary engineering resulting in control over grain size from 200 nm to 3 nm. Recently a new method is invented to deposit nanocomposite coatings for hard chrome replacement with control over inert particle content in coating depending upon application requirement. The new nanocomposite demonstrated excellent wear and corrosion resistance in comparison with hard chrome and commercial NIKASIL coatings. The process is economical and effortlessly scalable to existing electroplating industry with low initial capital investment.
Key Features
- Non line of site process, economical and ecofriendly
- Porosity free finished product, higher production rates
- Control over microstructure, mechanical properties, particle content in composite coating
- Higher current efficiency and deposition rates compared to traditional hard chrome process
- Easy technology transfer from research lab to existing infrastructure
Potential Applications
- Corrosion resistance and decorative coatings: automobiles include car, truck trim, motorcycle, kitchen and bathroom appliances
- Wear resistance: hydraulic actuators, railway engine shafts, aircraft landing gears, shaft journals, farm machinery, earth movers, snow plows, road repair equipment, mining equipment, automobile engine valves
- Industrial tools such as rolls for Al and steel manufacturing, stamping tools and dies, molds for plastic manufacturing utilized chrome plating for increasing its (tool) life
Intellectual Property Development Indices (IPDI) 
- Performance and stability are validated at laboratory and industry scale
- Scale-up version is also available up to 500 cm2 for industrial component
Status | 1 | 2 | 3 | 4 | 5 | 6 | 7 | 8 | 9 | 10 |
Major Patents / Publications
Major Publications
- An improved method for preparing nickel electrodeposit having predetermined hardness gradient (Indian Patent: IN200901455-I1)
- A method and an apparatus for preparing nickel tungsten based nanocomposite coating deposition (Indian Patent: 201611001190)
- Nitin P. Wasekar et al., Materials and Design, 112 (2016) pp. 140-150, Applied Surface Science, 364 (2016), pp. 264-272, Surface and Coatings Technology, 291 (2016) pp. 130-140, Materials Characterization, 116 (2016) pp. 1-7, Wear 342 (2015) pp. 340-348.
Hybrid Precursor Powder Plasma Spray Technology
Overview
Hybrid processing involves depositing layered or composite coating architecture using sequential or simultaneous feeding of powder and liquid feedstock, respectively. Independently controlled micron sized powder feedstock and liquid precursor solution are fed into the plasma spray plume to form the desired coatings. The concept is extremely convenient to adopt, as it involves only a minor modification in the injection arrangement in any existing thermal spray facility.
Key Features
The concept of hybrid processing opens up possibilities for depositing coatings with diverse architecture- Layered coatings by sequential feeding of liquid and powder feedstock
- Composite coatings by simultaneous feeding of liquid and powder feedstock
- Graded coatings by simultaneous feeding of liquid and powder feedstock, while continuously varying the feed rates of one or both feedstock.
Potential Applications
- Composite YSZ based TBCs for gas/steam turbine applications
- Composite alloy/metallic + ceramic coatings for wear resistance
- Oxide dispersed coatings for elevated temperature applications
Intellectual Property Development Indices (IPDI) 
- Developed wide ranging functional coatings for diverse industrial applications
- Prototype demonstration of various coatings is in progress
Status | 1 | 2 | 3 | 4 | 5 | 6 | 7 | 8 | 9 | 10 |
Major Patents / Publications
Major Publications
- G. Sivakumar and S.V. Joshi, ‘An improved hybrid methodology for producing composite, multi-layered and graded coatings by plasma spraying utilizing powder and solution precursor feedstock’, Indian Pat. No. 2965/DEL/2011 dt. 17th Oct, 2011
- A. Lohia, G. Sivakumar, M. Ramakrishna and S.V. Joshi, “Deposition of Nanocomposite Coatings employing a Hybrid APS + SPPS Technique”, Journal of Thermal Spray Technology, 23(7), 1054-1064, 2014
- S.V. Joshi and G. Sivakumar, Hybrid processing with powders and solutions: A novel approach to deposit composite coatings, Journal of Thermal Spray Technology, 24 (7), pp. 1166-1186, 2015
Micro Arc Oxidation Coating Technology
Overview
Micro Arc Oxidation (MAO) also known as Plasma Electrolytic Oxidation (PEO) is a novel and environmental friendly way of creating dense, ultra-hard (peak hardness up to 1800 HV) ceramic composite coatings for enhancing the wear, corrosion, electrical and thermal protection of Al alloys. MAO is an electro-chemical and electro-thermal oxidation in an alkaline electrolyte and the surface oxidation is driven by the supply of high voltage (up to 600 V) pulsed AC power. MAO coatings deposited on a large variety Al alloys such as 3-times harder, 15 times wear resistant and 10 times corrosion resistant than the hard anodized layers. Further, MAO technology can treat the difficult to anodize class of alloys such as Al-Si cast products. Through rigorous R&D activities pursued over last 2 decades, ARCI has mastered over the MAO process including the equipment design, building, testing, supply, installation and commissioning of academic scale, lab scale and industry scale systems with custom built capacities and capabilities.
Key Features
- Custom-built technology systems are available in large power supply ranges between 20 to 500 kVA depending upon the scale of operations
- Apart from a variety of Al alloys, coatings can also be formed on metallic components made out of Mg, Ti, Zr and their alloys
- It is possible to engineer the coating composition through additives added to the electrolyte depending upon the functional requirements of various industrial components
- Coating hardness increases with increasing thickness due to concurrently increased alpha alumina phase in the coating structure
Potential Applications
- Taking advantage of enhanced fatigue strength in addition to the wear, corrosion, thermal and electrical protection, numerous applications ranging from automotive, aerospace, wire drawing and textile industry are the potential segments
- Although the MAO process is discrete, continuous coating deposition technology developed on the basic platform of MAO coating formation is useful for providing an insulating coating on foils and wires of kilometre long is useful for electrical and electronics application.
Intellectual Property Development Indices (IPDI) 
- Prototype models of academic and industry scale systems were already fabricated, tested and demonstrated on a variety of applications, installed at customer locations.
- Application development for various industry segments is currently in progress to promote more technology transfers to the Indian industries and universities.
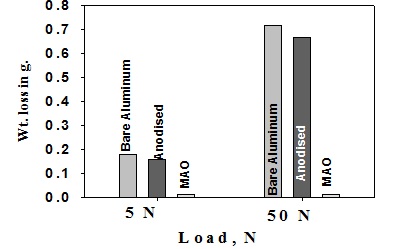
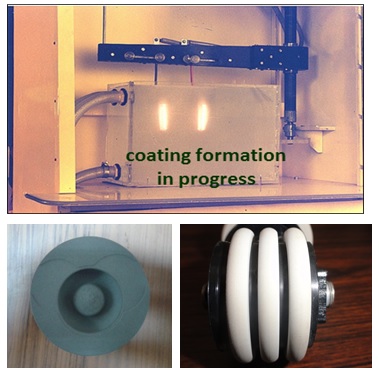
Status | 1 | 2 | 3 | 4 | 5 | 6 | 7 | 8 | 9 | 10 |
Major Patents / Publications
Major Patents*
- Indian Patent Applications: (a) 209817, (b) 1828/DEL/2008/01082008, (c) 1839/DEL/2015, US Patent Applications: (d) 6,893,551, (e) 8,486,237, (f) 9,365,945 UK Patent Application: (g) GB2464378, Japan Patent No: (h) 5442386, German Patent No: (i) 10 2009 044 256, French Patent Application: (j) 0957102, Brazil Patent No: (k) Pl0904232-6 A2 and South Africa Patent No: (l) ZA200906786.
Major Publications
- L. Rama Krishna et. al., Surface and Coatings Technology, vol. 163-164, 2003, pp. 484-490, Wear, vol. 261, 2006, pp. 1095-1101, Surface and Coatings Technology, vol. 167, 2003, pp. 269-277.
- L. Rama Krishna et. al., Metallurgical and Materials Transactions A, vol. 38, 2007, pp. 370-378, Surface and Coatings Technology, vol. 269, 2015, pp. 54-63, Journal of Alloys and Compounds, vol. 578, 2013, pp. 355-361.
Advanced Detonation Spray Coating Technology (DSC) MARK-II
Overview
With an overall objective of enhancing the efficiency, productivity and reliability by increasing the detonation frequency (more than 3Hz) of the existing DSC system, design of various critical parts and its integration with the existing system has been initiated. Accordingly, one DSC advanced system has already been fabricated and subjected to thorough testing with regard to functional aspects and resulting coating quality. Towards design and development of such an advanced DSC system, major challenges such as modification of existing mixing chamber, elimination of numerous mechanically moving parts such as cam, gear, piston, roller, bearings, re-engineering of solenoid valves, flashback arresters, mass flow controller, PLC computer controlled system have been successfully accomplished. Subsequent to the integration of all newly designed and re-engineered parts with the main assembly system, numerous coatings were generated at higher detonation frequencies such as 6Hz, process parameters were optimized to achieve the bench mark coating quality. The new system with enhanced functional features and increased productivity and reliability will be transferred to the existing technology receivers and also to the other industries.
Key Features
- High productivity due to high pulse frequency
- Less maintenance: absence of mechanically moving parts
- Good adhesion strength (>10000 psi)
- Dense microstructure (< 1%)
- Negligible thermal degradation and excellent tribological properties
- Ability to coat wide range of powders, carbide, oxide, metal powders
- Lower substrate temperature & low oxide content
- Coatings with 50-2000 microns thickness can be produced
Potential Applications
- Steel industry application such as Bridle rolls
- Textile & Paper industry applications such as wire passing pulleys, plungers, steeped cone pulleys, bearing stopper plates, guide rolls
- Gas compressor applications such as spindle valve, compressor disc, compressor shaft
- Strategic applications like HP & LP turbine blades, compressor discs, LCA nozzles, thrust beating sleeves, propeller shaft seals.
- Power and Energy applications such as guide vanes, spindle valves, hydro turbine blades.
Intellectual Property Development Indices (IPDI) 
- Process parameters were optimized, coating quality, repeatability and reliability studies were completed
- Subsequent to the technology launch, new systems will be fabricated, inspected, tested and transferred to the interested industries
Status | 1 | 2 | 3 | 4 | 5 | 6 | 7 | 8 | 9 | 10 |
Major Patents / Publications
Major Publications
- D. Srinivasa Rao et al, Detonation Sprayed Coatings for Aerospace Applications, in “Aerospace Materials and Material Technologies”, Ed: N.E. Prasad, R.J.H. Wanhill, Pubs: Indian Institute of Metals Series, Springer Science + Business Media, Singapore, 2017, pp: 483-500, ISBN: 978-981-10-2143-5, Article DOI: 10.1007/978-981-10-2134-3_22.
- D.Srinivasa Rao et al, “Detonation Sprayed Coatings and Their Tribological Performance” in Thermal Sprayed Coatings and Their Tribological, M. Roy, & J. Davim (Eds.) Thermal Sprayed Coatings and their Tribological Performances, IGI Global, 2015. (pp. 294-327). Hershey, PA: Engineering Science Reference. doi:10.4018/978-1-4666-7489-9.ch010
High Pressure Cold Spray Technology
Overview
Cold gas dynamic spray (also called Cold Spray or Kinetic Spray) involves accelerating micron sized powder particles to supersonic velocities resulting in the formation of dense, thick and pure coatings with high deposiotion rates. Cold spray is a low temperature high velocity variant of thermal spray family. This technique has very high deposition rates and deposition efficiencies. Since there is no heating of powders, retention of powder properties in the coating is possible. Dense coatings with porosity less than 0.1% can be achieved. Metallic, Alloy, Composites, Nanostructured and Amorphous powders can be deposited. This technology has huge potential for repair and refurbishment, electrical and thermal applications. The uniqueness is to target dense coatings that need very high particle velocities to get deposited using cold spray and to deposit dense coatings of Refractory Metals, Molybdenum, Cobalt based materials, superalloys, metal-metal carbide composites without having to resort for a post treatment procedure.
Key Features
- Indigenously developed state of the art PLC based automated Portable control panel (Max Pressure – 100 bar)
- High Mach Number Nozzles (>3)
- Maximum Pressure-50 bar; Maximum Temperature-600oC
- Steels, Super Alloys, Molybdenum, HEAs, Refractory coatings
- Indigenously designed and fabricated High Pressure Heater
- Indigenously designed and fabricated High Pressure Gun and Powder Feeder
- Indigenously desined and fabricated high mach number nozzles
Potential Applications
- Repair and Refurbishment Applications
- Coatings for Electrical contacts, lugs, EMI shielding, heat sinks
- Coatings for High Temp Corrosion resistance, Bio medical, Sputter Target
- Super Alloy coatings for high temperature wear and corrosion applications
- Wear resistant coatings (Metal-Metal Carbides)
- Nanostrcutured / amorpohous/ BMG coatings
- High Entropy Alloy Coatings for Bondcoats for High Temperature Gas Turbine Apploications Applications
Intellectual Property Development Indices (IPDI) 
- Preliminary Process Development Level
Status | 1 | 2 | 3 | 4 | 5 | 6 | 7 | 8 | 9 | 10 |
Major Patents / Publications
Major Publications
- Naveen M Chavan, SP Phani, M Ramakrishna, DS Rao and G Sundararajan, Surface & Coatings Technology 205 (2011), P4798–4807
- G Sundararajan, Naveen M Chavan and S Kumar, Journal of Thermal Spray Technology, 1348—Volume 22(8) December 2013
- S Kumar, A.Jyothirmayi, Nitin Wasekar and SV Joshi, Surface and Coatings Technology, 296(2016), 124-135
Detonation Spray Coating Technology (DSC)
Overview
DSC is a thermal spray process capable of producing coatings with extremely good adhesive strength, and low porosity with compressive residual stresses. Metered proportion of the combustion mixture comprising of oxygen and acetylene (oxy-fuel: OF ratio) is fed through a tubular barrel closed at one end. The gas mixture inside the chamber is ignited by a simple spark plug and the combustion generates high pressure shock waves (detonation wave), which then propagate through the gas stream. Simultaneous admission of the coating powder fed into the combustion chamber results in particle acceleration while the temperature of the hot gas stream can go up to 4000 deg C depending on the OF ratio employed. The hot gases generated in the detonation chamber while travelling down the barrel at a high velocity rapidly heats the particles to a plasticizing stage (skin melting) and also accelerate the particles to a velocity of 800-1200m/sec. These particles then come out of the barrel and impact the component surface to form the coating. The high kinetic energy of the semi-molten powder particles upon impact with the substrate result in formation of a very dense coating. The chamber is finally flushed with nitrogen to clean the barrel for subsequent detonation cycle to obtain thicker coatings. Depending on the required coating thickness and the type of coating material, the detonation spraying cycle can be repeated at the rate of 3 shots per second.
Key Features
- Good adhesion strength (>10000 psi)
- Dense microstructure (< 1%)
- Negligible thermal degradation
- Good surface finish (~4-6 mm Ra)
- Ability to coat wide range of powders
- Lower substrate temperature & low oxide content
- Good tribological properties
- Coatings with 50-2000 microns thickness can be produced
Potential Applications
- Steel industry application such as Bridle rolls
- Textile & Paper industry applications such as wire passing pulleys, plungers, steeped cone pulleys, bearing stopper plates, guide rolls
- Gas compressor applications such as spindle valve, compressor disc, compressor shaft
- Strategic applications like HP & LP turbine blades, compressor discs, LCA nozzles, thrust beating sleeves, propeller shaft seals.
- Power and Energy applications such as guide vanes, spindle valves, hydro turbine blades.
Intellectual Property Development Indices (IPDI) 
- Multiple number of prototype industry scale systems were thoroughly tested and transferred to technology receivers across the country
- Coating production using DSC is fully streamlined (Arial Narrow 10 pt – Not more than 3 bullet points of one line)
Status | 1 | 2 | 3 | 4 | 5 | 6 | 7 | 8 | 9 | 10 |
Major Patents / Publications
Major Publications
- D. Srinivasa Rao et al, Detonation Sprayed Coatings for Aerospace Applications, in “Aerospace Materials and Material Technologies”, Ed: N.E. Prasad, R.J.H. Wanhill, Pubs: Indian Institute of Metals Series, Springer Science + Business Media, Singapore, 2017, pp: 483-500, ISBN: 978-981-10-2143-5, Article DOI: 10.1007/978-981-10-2134-3_22.
- D.Srinivasa Rao et al, “Detonation Sprayed Coatings and Their Tribological Performance” in Thermal Sprayed Coatings and Their Tribological, M. Roy, & J. Davim (Eds.) Thermal Sprayed Coatings and their Tribological Performances, IGI Global, 2015. (pp. 294-327). Hershey, PA: Engineering Science Reference. doi:10.4018/978-1-4666-7489-9.ch010
Electron Beam Physical Vapour Deposition System (EBPVD)
Overview
EBPVD technology is known to deposit the coatings with columnar microstructure which results in enhanced strain tolerance and erosion resistant at high temperatures. Owing to this specific technological feature, EBPVD coatings are popularly employed for depositing the ceramic coatings with extremely lower thermal conductivity. One of the best known configurations of such thermal barrier coating (TBC) is the top coat of yttria stabilized zirconia (YSZ) with a suitable bond coat on aero engine gas turbine blades and vanes. Further, EBPVD technology is also suitable for depositing a wide variety of metallic, alloy and composite materials which is also suitable for the bond coat applications such as MCrAlY (M = Ni or Co) on the super alloy substrates for enhanced functional performance. Such an EBPVD technological unit with specific features and special capabilities has been established at ARCI in collaboration with M/s International centre for Electron beam technologies, Kiev, Ukraine for readily serving the Indian industry. The EBPVD consisting of multiple EB guns which will melt and evaporate the ingot materials under specific vacuum conditions in a controlled chamber wherein the vaporised materials get subsequently deposited on the substrate materials. Specialized jigs and fixtures were designed and processing parameters were optimized to provide the TBC’s on a variety of components needing protection against the high temperatures. In addition, an innovative methodology has been created to benefit the Indian strategic sector and industry for refurbishing and repairing a variety of blades and vanes indigenously during engine’s periodic overhauls thus saving notable amount of foreign currency.
Key Features
- Coatings obtained are dense, uniform and smooth
- Possible to obtain gradient compositions, structure and properties as required
- 50-100 µm/hr deposition rate with a productivity of 10-15 kg/hr
- Large window of coating thickness (10μm-2 mm)
- Ability to coat thin foils, strips, sheets & heavy blanks
Potential Applications
- By changing the processing conditions such as ingot composition, part manipulation and EB energy, EB-PVD technology is capable of depositing various coatings such as: functional gradient coatings, multilayered thick ceramic coatings, textured multilayer coatings, biological coatings
- Hot Corrosion & Oxidation Resistant Coatings
- Uniform Thermal Barrier Coatings (TBCs)
- Damping and Wear Resistant Coatings
- Thick Repair Coatings up to 1-2 mm
Intellectual Property Development Indices (IPDI) 
- Application development in aero engine and power sector turbine blade and sponsored project on development of TBC coating rotor HP rotor turbine blades for helicopter engine is currently in progress at ARCI.
Status | 1 | 2 | 3 | 4 | 5 | 6 | 7 | 8 | 9 | 10 |
Major Patents / Publications
Major Publications
- D. Srinivasa Rao et al, Processing-Structure-Property Relationships in EB-PVD Yttria Stabilized Zirconia (YSZ) Coatings, Journal of Vacuum Science & Technology A 29, 2011
- Dipak K. Das, D.Srinivasa Rao et al, Singh, Microstructure, Texture and Thermal Cycling Performance of EB-PVD TBCs Deposited under Different Processing Conditions, Journal of High Temperature Materials and Processes, Vol.30(2011),pp.539-548