Other Industries
Pressure slip casting of complex shapes of Advanced Ceramics
Overview
Pressure slip casting, a well known technique in practice for the table ware production has not yet been considered as a potential and productive method production for Advanced Ceramics. The PCS 100N (SAMA GmbH) has been worked upon to produce Advanced Ceramics products, initially that of Al2O3. The machine parameters have been stabilized and the optimization of slip preparation with local brands of Al2O3 has been successfully done to produce dense discs of sintered densities greater than 98%. The sintered discs of dia 70 mm and thickness >5 mm with above densities have been reproducibly produced on PCM to gain confidence. Reasonable expertise to prepare required polymer moulds suitable to be used on PCM to pressure cast desired shapes and dimensions has also been acquired during these trials. Polymer moulds prepared to pressure cast shapes like spools, solid spheres, one end closed tubes and successfully used on the PCM with Al2O3 slips. The work to make more complicated advanced ceramics like channelled (b/b) slabs, long cones, large slabs etc is in progress. Pressure casting of full solid spheres of Al2O3 with 60 mm dia and 60% green density is achieved successfully.
Key Features
- Highly productive with a possibility of almost 30 cycles/hr depending on the slip and product
- Yields 58%-60% green density and consistency is assured
- Easily up scalable to meet the industrial/commercial requirements
- Many complex shapes and structures can be easily pressure cast using aqueous slips
- Polymer moulds can be used to produce at least 15000-20000 cast cycles
- Eco-friendly with minimum rejection (3% max.)
- Polymer mould fabrication can be a part of the PC technology
- Requires min man power. Can be automated if required
Potential Applications
- Manufacturing of advanced ceramics with complicated shapes, one end closed tubes, grinding media etc. with high productivity for commercialization
Intellectual Property Development Indices (IPDI) 
- Technology for wear resistance alumina grinding balls demonstrated and undergoing field trials
- Polymer mould fabrication for required shapes established
- Pressure casting of alumina ceramic established for various shapes and dimensions
- IPDI level: 6
Status | 1 | 2 | 3 | 4 | 5 | 6 | 7 | 8 | 9 | 10 |
Major Patents / Publications
Major Patents
- Inter Ceram 62 2013 (3) 221-223
Extrusion processing of complex shaped ceramic tubes and honeycombs
Overview
Extrusion processing which involves the shaping of a visco-plastic formable paste through a specially designed die is the most commonly used technique used for the manufacture of honeycombs and tubes. The honeycomb extrusion is a complex process involving lateral flow of the dough followed by the knitting with adjacent cross section within the die the rheological properties of the dough play a major role. Because of the flexibility in tailoring, honeycombs can be engineered to exhibit a unique combination of mechanical and thermal properties for diversified thermo structural applications Rheological properties depends on a variety of factors such as the choice of the binder, the extent of solids loading in the dough, the particle characteristics of the ceramic powder used, etc.
Key Features
- Extrusion process for wide range of ceramic formulations
- Low expanding honeycomb cellular ceramics
- Thin walled porous and dense tubes
- Ram and Screw type extrusion processes
- Capability to design and fabricate in-house dies including for honeycombs
- Optimized heat treatment schedules based on the ceramic formulation
- Engineered structural, thermal and mechanical properties
Potential Applications
- Kiln Furniture and furnace fixtures
- Honeycomb substrates for catalysis
- Energy absorption, conservation and generation
- Environmental protection
Intellectual Property Development Indices (IPDI) 
- Patented In-house honeycomb die fabrication technology in collaboration with Samara State University, Samara
- Ready to demonstrate extrusion process
- Extrusion technology for porous and dense tubes
Status | 1 | 2 | 3 | 4 | 5 | 6 | 7 | 8 | 9 | 10 |
Zirconia/MgO ceramics with engineered porosity for thermal management /high chemical inert applications
Overview
Engineered porosity plays an important role in achieving low thermal conductivity and hence on insulating performance. However, the loss of strength becomes an important disadvantage with increasing porosity. Quantity of porosity along with the tailored pore size becomes critical to choose an optimum as these properties conflicts each other. Methodologies are successfully developed to fabricate zirconia ceramics with optimum porosity and strength for thermal management applications.
Key Features
- Low thermal conductivity (<1W/m-K)
- Highly stable cubic structure
- Engineered porosity through fugitive pore formers
- Moderate mechanical strength through optimum pore size distribution
- Stability and durability in harsh environments
- Capability for complex shaping
Potential Applications
- Self standing ceramic parts for insulation
- High temperature insulation up to 1500oC
Intellectual Property Development Indices (IPDI) 
- Key parameters demonstrated on coupon level
- Formulation finalized and Heat treatment schedules optimized
- Scale up trials are in progress
Status | 1 | 2 | 3 | 4 | 5 | 6 | 7 | 8 | 9 | 10 |
Major Patents / Publications
Major Patents
Major Publications
Reticulated Ceramic Foam Structures
Overview
Ceramic foams are three-dimensional frame work with high porosity forming a tortuous system of interconnected cells and channels. Ceramic foams because of their inherent reticulated structure widely used as molten metal filters, catalyst supports, flame arrestors etc. Ceramic reticulated open cell foams are commonly processed by a polymer sponge processing.
Key Features
- Engineered pore densities, formulations, dimensions and shapes
- Flexibility in process to achieve desired thermo- mechanical properties
- Low pressure drop in combination with tortuous path
- Light weight ceramics
Potential Applications
- Substrates for solar thermal applications
- Bio-medical scaffolds
- Catalyst substrates for pollution control
- Hot gas and molten metal filters
Intellectual Property Development Indices (IPDI) 
- Polymeric sponge processing is established for various ceramic formulations
- Capability to develop the process based on the application
Status | 1 | 2 | 3 | 4 | 5 | 6 | 7 | 8 | 9 | 10 |
Major Patents / Publications
Major Publications
- Quasi-static compression behavior of nickel oxide, nickel oxide: zirconia, nickel:zirconia and nickel foams, Ceramics International, 42 (2016) 10572–10578
- Development of Cordierite based Reticulated Foams with Improved Mechanical Properties for Porous Burner Applications, Transactions of Indian Ceramic Society (In press)
Fabrication of free standing ceramics through Chemical Vapour Deposition
Overview
Chemical Vapour Deposition process developed using the reaction between zinc and hydrogen sulphide to produce stoichiometric zinc sulphide (ZnS). A technology of producing complex or simple shaped substrates for the CVD deposition depending on the target requirements is patented. Post processed CVD ZnS samples have shown close to theoretical values with respect to thermal, mechanical and transmission properties.
Key Features
- Theoretically dense
- Near net shape
- High homogeneity
- Thickness building upto 10mm
Potential Applications
- IR imaging
- Optical ceramics
Intellectual Property Development Indices (IPDI) 
- IPDI level: 10 for ZnS
Status | 1 | 2 | 3 | 4 | 5 | 6 | 7 | 8 | 9 | 10 |
Major Patents / Publications
Major Publications
- Effect of post CVD thermal treatments on crystallographic orientation, microstructure, mechanical and transmission Properties of ZnS Ceramics, Journal of Alloys Compounds, 496 (2010) 273-277
- Effect of Sphalerite to Wurtzite Crystallographic Transformation on Microstructure, Optical and Mechanical Properties of Zinc Sulphide Ceramics, Ceramic International, 37 (2011) 1039-1046
Gel Casting of Complex Shaped Ceramics
Overview
Gel casting process involves solidification of ceramic slurries by the free radical initiated polymerization of a chain forming monomer with a cross linking monomer in presence of a catalyst. Specific advantages such as high solid loading (50-55 vol %), instant solidification (15-60 min) and uniform green microstructure enabling green machining. However, acrylamide based gel casting process suffers from the serious drawback of being toxic as a result of which its use on a wide spread commercial scale has been limited. In view of this an environmentally benign nontoxic polymeric such as methyl cellulose, which undergo thermally induced gelation at temperatures in the range of 70-80°C has also experimented for shaping.
Key Features
- Acrylamide based gelation through polymerisation process
- Environmental friendly methyl cellulose based thermal gelation
- Flexibility in polymer selection for the desired green strength
- Near net complex shaping
- Possibility of green machining of parts, if required
Potential Applications
- Shaping of near net shaped complex ceramic parts
Intellectual Property Development Indices (IPDI) 
- Processing steps optimised
- Capability to produce complex shapes
Status | 1 | 2 | 3 | 4 | 5 | 6 | 7 | 8 | 9 | 10 |
Hot Isostatic Consolidation of Vacuum Encapsulated Ceramic Powders
Overview
Ceramic powders encapsulated specially designed metallic can using an encapsulation welder under 10-3 Torr at elevated temperatures. The encapsulated capsule was subjected to direct consolidation by Hot Isostatic Pressing (HIP) at desired temperatures and pressures. Deformed capsule after HIP cycle was machined to release the dense compact. In a typical experiment with alumina ceramics samples was found to attain a density of 3.94 g/cc and a flexural strength of 310 MPa at a relatively low temperature of 1350oC in a single step of HIP consolidation.
Key Features
- Expertise to design cans based on the part geometry
- Engineered HIP parameters based on formulations
- Single step densification process
- Theoretical densities
- Scalable process
Potential Applications
- Fabrication of theoretically dense ceramic components
- Complex and simple geometries
Intellectual Property Development Indices (IPDI) 
- Process established on a laboratory level
- Scale-up and prototype module fabrication is in progress
Status | 1 | 2 | 3 | 4 | 5 | 6 | 7 | 8 | 9 | 10 |
Major Patents / Publications
Major Patents
Major Publications
- Vacuum Encapsulation of Sub-μm Alumina Powder and Densification by Direct Consolidation through Hot Isostatic Pressing, International Conference on Advance in Materials and Manufacturing, 8-10 December-2016.
Radiant Porous Burners
Overview
Increasing concern on fossil fuel depletion has paved a way for the energy efficient and eco-friendly energy management technologies in various vital sectors. Porous Medium Combustion through reticulated foam structures is considered to be one of the feasible options which got explored extensively in the industrial and domestic applications. A wide variety of ceramic foams are developed and explored for porous burner applications.
Key Features
- Ceramic foam based Porous Combustion
- High energy efficiency
- Environmental friendly
- Short start-up time
Potential Applications
- Energy efficient burning of gaseous fuels
- Industrial radiant burners
Intellectual Property Development Indices (IPDI) 
- Concept proved on a laboratory scale
- Scale-up and prototype module fabrication in progress
Status | 1 | 2 | 3 | 4 | 5 | 6 | 7 | 8 | 9 | 10 |
Major Patents / Publications
Major Publications
- Development of Cordierite based Reticulated Foams with Improved Mechanical Properties for Porous Burner Applications , Transactions of the Indian Ceramic Society-2016- In Press
Development of Transparent Ceramics
Overview
Transparent ceramics, a new class of advanced functional materials, find diverse applications in strategic and civilian sectors owing to the unique combination of mechanical and transmission properties. Technological advancements in ceramic powder synthesis, shaping and sintering have made it possible to tailor the microstructural, mechanical and optical property relationships in case of advanced transparent ceramic materials. Transparent ceramic materials are classified broadly as visible, mid wave and long wave infrared regions.
Key Features
- Capability to fabricate polycrystalline transparent ceramic specimens of transparent alumina, aluminium oxynitride (AlON), spinel (MgAl2O4) through slip casting and Hot Isostatic Pressing
- Capability to fabricate transparent zinc sulphide (ZnS) ceramics through Chemical Vapour Deposition (CVD)
- Specific parameters depends on ceramic formulation
Potential Applications
- Dental Ceramics and Artificial Gem Stones
- Solar Absorber Tubes and Lamp Envelops
- IR sensor envelops
- High temperature Furnace windows
Intellectual Property Development Indices (IPDI) 
- Process steps optimised to achieve theoretical transmissions
- IPDI level
- ZnS: 10
- Magnesium aluminate spinel: 10
Status | 1 | 2 | 3 | 4 | 5 | 6 | 7 | 8 | 9 | 10 |
Major Patents / Publications
Major Publications
- Optical and mechanical properties of compaction and slip cast processed transparent polycrystalline spinel ceramics, Ceramics International 40 (2014) 5575–5581
Electrochemical Synthesis of Lithium Aluminium Hydride an advanced Propellant Ingredient
Overview
In recent years, high performance solid propellant has been a great deal of attention in the area of high energy materials research field. Development of a high performance solid propellant will be achieved by using high energy density materials such as metal hydries. Among the metal hydrides, aluminium Hydride, AlH3, commonly known as alane is the most interesting fuels for propulsion, because of its ability to substantially increase the performance of a given system. The typical formation route of alane is through the chemical reaction. It involves high pressure operation and formation other by products like metal halide. For these reasons, our research attempt has been initiated in a more economically and thermodynamically cost effective synthetic and regeneration route to produce alane by electrochemical method.
Key Features
- Avoid the impractical high pressure needed to form AlH3
- Avoid chemical reaction route of AlH3 that leads to the formation of alkali halide salts such as LiCl or NaCl
- Utilize electrolytic potential to translate electrochemical potential into chemical potential and drive chemical reactions to form AlH3
Potential Applications
- As an additive in solid propellant
- On-board Hydrogen Storage
Intellectual Property Development Indices (IPDI) 
- Setting up electrochemical facility for synthesis of alane
- Preliminary single cell studies for alane preparation.
Status | 1 | 2 | 3 | 4 | 5 | 6 | 7 | 8 | 9 | 10 |
Major Patents / Publications
Major Patents
Major Publications
- Aluminium Hydride as an advanced propellant Ingredient- A synthesis perspective G.T.Harini, T.Ramesh R. Balaji, N. Rajalakshmi, V. Venkatesan, S.Nandagopal . Paper Presented at Advanced Materials and Processes for defence applications (ADMAT19) on Sep 23-25’2019 at Hyderabad
Electrochemical Methanol Reformation (ECMR) for Hydrogen Generation
Overview
The successful commercialization of Fuel cell technologies requires steady hydrogen supply. Steam Reformation of hydrocarbons and electrolysis of water are commonly available methods to produce hydrogen. However steam reformer works best in higher capacity systems, while the electrolysis requires more energy input for splitting water to hydrogen and oxygen due to its high over potentials. CFCT has now developed a method which combines aspects of both the processes to produce hydrogen from methanol - water mixture. The Centre has developed and demonstrated of a hydrogen generator of 1 Nm3 hydrogen per hour capacity. Currently, the development of 2.5 Nm3/hr PEM based ECMR with improved performance and reduced cost is under progress.
Key Features
- Energy consumption for Hydrogen production was found to be low, about 1/3rd of water electrolyzer.
- Hydrogen can be produced at much lower temperature and pressure, unlike methanol reformer
- The hydrogen produced is highly pure and Hydrogen separation steps are not required.
- Carbon based materials can be used for stack fabrication
Potential Applications
- ECMR can be integrated with renewable energy sources like wind, solar to store the energy in the form of hydrogen and it can be used in fuel cells.
- In Power station as coolant
- In Semiconductor industry as a reducing agent
- Meteorological Department (hydrogen as a lift gas to fill weather balloons.
Intellectual Property Development Indices (IPDI) 
- Scaled-up from single cell to stack and prototyp system developed and demonstrated
- Performance was tested for extended duration at laboratory
Status | 1 | 2 | 3 | 4 | 5 | 6 | 7 | 8 | 9 | 10 |
Major Patents / Publications
Major Patents
Major Publications
- Exfoliated Graphite separator based Electrolyzer for Hydrogen generation”. K.S.Dhathathereyan, R.Balaji, K.Ramya, N.Rajalakshmi, L.Babu, R.Vasu, P.Sarangan, R.Parthasarathy, Indian Patent Application no. 3073/DEL/2013.
- Method of preparing gas diffusion layer for the electrode of ECMR cell for hydrogen generation” R.Balaji, N.Rajalakshmi, K.Ramya, R.Vasudevan, K.Sudalayandi, Indian Patent Application No: 201911030852
- Influence of ethyl acetate as a contaminant in methanol on performance of Electrochemical Methanol reforming (ECMR) for hydrogen production. N.Manjula, R.Balaji, K.Ramya, N.Rajalakshmi K.S.Dhathathereyan, A. Ramachandraiah, Int. J.Hydrogen Energy, 43(2) 2018, 562-568.
- Electrochemical methanol reformation (ECMR) using low cost sulfonated PVDF/ZrP membrane for Hydrogen Production,N.Manjula, R.Balaji, K.Ramya, N.Rajalakshmi K.S.Dhathathereyan, A. Ramachandraiah, Journal of Solid State Electrochemistry, Vol.22, P 2757-2765, 2018.
- Nitrogen doped graphene supported Pd as hydrogen evolution catalyst for electrochemical methanol reformation” Manjula Narreddula, R. Balaji, K. Ramya, N. Rajalakshmi, A. Ramachandraiah. Int. Journal of Hydrogen Energy, Vol.44, P4582-4591,2019.
- Hydrogen Production by Electrochemical Methanol Reformation using Alkaline Anion Exchange Membrane based cells. Manjula Narreddula, R. Balaji, K. Ramya, N. Rajalakshmi Int.J.Hydrogen Energy, Vol.45, P 10304-10312, 2020
- A Polymer Electrolyte Membrane (PEM) cell and a method of producing hydrogen from aqueous organic solutions in pulse current mode” K.S.Dhathathreyan, R.Balaji, K.Ramya, N.Rajalakshmi. Indian Patent Application no. 3313/DEL/2012
- Studies on development of Titanium oxide Nano Tube (TNT) based ePTFE–Nafion–composite membrane for electrochemical methanol reformation, N.Manjula, R.Balaji, K.Ramya, K.S.Dhathathereyan,A.Ramachandraiah Int. J.Hydrogen Energy, 41 2016, 8777- 8784. 3.
- Palladium Nanoparticles as Hydrogen Evolution Reaction (HER) electrocatalyst in Electrochemical Methanol Reformer K. Naga Mahesh, R. Balaji, K.S. Dhathathreyan. Int.J.Hydrogen Energy 41, 2016, 46-51
PEM fuel cell based power supply systems
Overview
Fuel cell are considered to be an ideal choice for power generation as the green house gas emission issues are considerably reduced.PEM Fuel cells are ideally suited for decentralized power generation due to their fast start up, modular nature and low start up temperature. The technological challenges include developing high performance fuel cell stacks and BoP components like the power conditioners, thermal management system etc. The successful commercialization of Fuel cell technologies requires steady hydrogen supply and development automated methods for key components fabrication. One of the aspects that is proposed to be undertaken is improved manufacturing methods . Rapid prototyping or Additive manufacturing has been considered in this project as the conventional methods of making the fuel cells is lengthy with lot of wastage.
Key Features
- Developed Grid Independent fuel cell systems in the range of 1-20kW power.
- PEM Fuel cells developed have been continuously operated for 500 hrs and intermittently for several thousand hours with stable performance.
- Suitable control systems for load following cycle, cell monitoring characteristics, power conditioners and thermal management have been developed.
Potential Applications
- As decentralised power pack for homes, industries etc.
- As combined heat and power units for homes
- As uninterrupted power source even when the power outage is for long duration ( >8hrs)
- As back up power for telecom industries.
Intellectual Property Development Indices (IPDI) 
- Scaled-up from single cell to stack and prototype system developed and demonstrated
- Performance was tested for extended duration at laboratory and industrial environment
Status | 1 | 2 | 3 | 4 | 5 | 6 | 7 | 8 | 9 | 10 |
Major Patents / Publications
Major Patents
Major Publications
- Sreeraj P, Raman Vedarajan, N.Rajalakshmi, Venkatasailanathan Ramadesigan, Screening of Recycled Membrane with Crystallinity as a Fundamental Property, International Journal of Hydrogen Energy
- An Improved Test Control System useful For Fuel Cell Stack Monitoring and Controlling, K.S. Dhathathreyan,N. Rajalakshmi, Indian Patent application no. 269/DEL/2013
- A Method of Preparation of Supported Platinum Nano Particle Catalyst in Tubular Flow Reactor Via Polyol Process, K S Dhathathreyan, N Rajalakshmi, K N M Krishna, 1571/DEL/2013
- S. Pandiyan, K. Jayakumar, N. Rajalakshmi and K. S. Dhathathreyan, "Thermal and Electrical Energy Management in a PEMFC Stack - An Analytical Approach", International Journal of Heat and Mass Transfer, Vol. 51(3-4), p 469-473, 2008
Development of Electrically Rechargeable Zinc-air Battery
Overview
Electrically rechargeable Zinc-air batteries exhibit high specific energy and interesting from an economical and ecological point of view. One of the challenges with Zn-Air batteries is to make them rechargeable in aqueous based system. Scientists at CFCT are addressing this issue and have initiated a program to develop rechargeable Zn-air battery and eventually other metal - air batteries. In the first instance, we have developed and demonstrated rechargeable 12 V Zn-Air battery using air breathing electrodes and ionic liquid electrolyte. The cyclic stability studies were also reported. Presently CFCT has initiated work on development of aqueous electrolyte based rechargeable Zinc-air secondary battery and carried out preliminary studies. The electrode area of the cell has been scaled up from 5 sq.cm to 30 sq.cm and results shows improved cycle life and capacity of the cell and it has provided the scope for further improvement, which is in progress.
Key Features
- High Energy Density
- Materials are low cost, non-toxic and environmentally friendly.
- Easy fuel storage
- Non-flammable and non-explosive nature
Potential Applications
- Smart and green grid storage
- Automobile (Electric Vehicle)
- Portable
Intellectual Property Development Indices (IPDI) 
- Performance and stability are validated at single cell level
- Scale-up and prototype module fabrication underway
Status | 1 | 2 | 3 | 4 | 5 | 6 | 7 | 8 | 9 | 10 |
Major Patents / Publications
Major Patents
Major Publications
- Karajagi, I., Ramya, K., Ghosh, P. C., Sarkar, A., Rajalakshmi, N., (2020) Nickel Integrated Carbon Electrodes for Improved Stability, Journal of Electrochemical Society 2020 167 130510.
- Karajagi, I., Ramya, K., Ghosh, P. C., Sarkar, A., Rajalakshmi, N., (2020) Co-doped carbon materials synthesized with polymeric precursors as bifunctional electrocatalysts, RSC Adv 2020,10, 35966-35978.
- Karajagi, I., Ramya, K., Ghosh, P. C., Sarkar, A., Rajalakshmi, N., (2019) . Ion Immobilized Bifunctional Electrocatalyst for Oxygen Reduction and Evolution Reaction, ACS Appl. Energy Mater. 2019, 2, 11, 7811-7822.
- Karajagi, I., Ramya, K., Ghosh, P. C., Sarkar, A., Rajalakshmi, N., (2019) Engineering of O2 Electrodes by Surface Modification for Corrosion Resistance in Zinc-Air Batteries, Springer Proceedings in Energy pp 717-723,Springer.com/gp/book/9789811559549.
- N.Sasikala, K.Ramya, K.S.Dhathathreyan, Bifunctional electrocatalyst for oxygen/air electrode Energy Conversion and Management. 77, 2014, 545-549.
Development and Manufacturing of metallic Flow field Plates for PEM Fuel cells
Overview
PEMFC technology has already been demonstrated in portable, stationary power, transport and several niche applications. For large scale commercialization technological advances are needed interms of cost reduction and manufacturing methods for producing some of the components. The major cost components are bipolar plates, catalyst and membrane. Bipolar plates facilitates the distribution of the reactants to the electrodes and presently constitutes about 50% of the cost ( for graphite plates ) and 75% of the weight and volume. Alternative materials to graphite and its composites are SS based metallic flow field plates which is likely to reduce the weight and volume by more than 50% as they can be made thinner unlike the graphite / carbon composite plates. The major challenge in developing the metal flow field plate lies in forming a complex flow field design on both sides of the plate for the supply of reactants and bond them together for proper sealing in case of multiple cells. An earlier study by ARCI led to the development of bipolar plates based on exfoliated graphite which reduced the machining cost of making bipolar plates.
Key Features
- Develop metallic bipolar plate by hydroforming technique with an industry partner after flow field and die design optimization
- Study of its corrosion properties under fuel cell conditions
- Development of suitable seals for optimum contact and prevent leakage of reactant gases.
- Development fuel cells and performance optimization at single cell and stack level.
Potential Applications
- Light weight PEMFC stack for vehicular applications
Intellectual Property Development Indices (IPDI) 
- Corrosion studies on various coated and bare metallic plates being studied.
- SS based bipolar plates stack was developed using conventional technology for development of seals.
Status | 1 | 2 | 3 | 4 | 5 | 6 | 7 | 8 | 9 | 10 |
Major Patents / Publications
Major Patents
- An Improved Process for the Preparation of Exfoliated Graphite Separator Plates useful in Fuel Cells, the Plates Prepared by the Process and a Fuel Cell Incorporating the Said Plates, K.S. Dhathathreyan,N. Rajalakshmi,S. Pandiyan patent application no. 1206/DEL/2006
Major Publications
Sodium Beta Alumina (NBA) Ceramics for Energy applications
Overview
Sodium beta alumina has been late seen as one of the highly potential candidates for battery and other electrolyte based applications due to firstly its high levels of sodium ion conductivity and secondly for the availability and the low price of the raw materials required to prepare the desired composition. Easier to make at the lab level to demonstrate the technical features but its physical and chemical properties like sensitive to humidity, water, high sintering temperatures, sodium evapouration, low densities achieved, limited shelf life and limitations in scaling up of powder production etc., have made it difficult to get absorbed by the industry for real device applications. ARCI has taken up two projects to develop sintered shapes of Sodium bet alumina for two entirely different applications where the prime feature exploited would be its ionic conductivity. Production of kilograms of the powder reproducibly and maintaining its phase purity by inert storing has been established. Fabrication and successful firing overcoming the issue of sodium evaporation to obtain tube and container shapes is achieved. Field trails and number production is due and in progress.
Key Features
- Sodium beta alumina powder synthesis established in kgs level via solid state routes
- Sodium evaporation issues solved
- Desired densities (>94%) achieved at 1650-1700 Deg C
- Shaping issues resolved- tubes, containers prepared through casting /CIP techniques
- Storage in inert way safeguarding the phase purity is established
- Making of shapes in numbers is in progress
Potential Applications
- Sodium ion based ionic conductor- A good electrolyte
- High energy battery applications
- Selective separation techniques based on its ionic conductivity
Intellectual Property Development Indices (IPDI) 
- Performance and stability are validated at laboratory scale
- Scale-up and prototype module fabrication underway
Status | 1 | 2 | 3 | 4 | 5 | 6 | 7 | 8 | 9 | 10 |
Advanced Carbon materials for Metal-ion Batteries
Overview
Carbonaceous nanomaterials have received a great interest as the anodes for metal-ion batteries (Sodium and Potassium-ion batteries) with regard to their excellent performance in lithium-ion batteries. Despite that, their unique structural properties and abundant availability makes them very interesting materials to enhance the performance of the batteries for large-scale energy storage applications. ARCI is focusing on the development of different types of advanced carbon materials for energy storage applications such as lithium-ion, sodiumion batteries and Supercapacitors. Mainly exfoliated/expanded graphite (with increased d-spacing) is superior anode material for sodium ion batteries, which allow the sodium ions into intercalation process and metal oxide/ carbon composites are high performance anode materials for metal-ion batteries (Lithium and Sodium)
Key Features
- Development of advanced carbon materials
- Synthesis of Graphene Nano platelets
- Development of metal oxide/carbon composites
- Activated carbon derived from bio-waste for high energy density based supercapacitor
- Carbon soot derived from solid waste
Potential Applications
- Automotive sector
- Portable Electronics
- Grid Storage
Intellectual Property Development Indices (IPDI) 
- Performance and stability are validated at laboratory scale
- Scale-up and prototype module fabrication underway
Status | 1 | 2 | 3 | 4 | 5 | 6 | 7 | 8 | 9 | 10 |
Major Patents / Publications
Major Patents
- The percentage for technology readiness level may be given strictly based on the indicators provided. In case of difficulty in shading (blue) the row in the table for 45%, 55% etc., it will be taken care at my end.
- The format for address at the bottom of page
- a. Name of the Centre
- b. Address of ARCI
- c. Telephone number format : Concerned Scientist/s followed by Team Leader's telephone number
- d. Email id format:Concerned Scientist/s, Team Leader and concerned Associate Director's email id.
- The content should not exceed one page.
- Only two images to be provided –(microstructure, product, graph or specific facility)
Major Publications
Solution Precursor Plasma Spray (SPPS) Technology
Overview
SPPS is an exciting method to produce a wide variety of functional oxide ceramic coatings, starting with appropriate solution precursors in contrast to powder feedstock in case of conventional plasma spraying. The technique utilizes aqueous/organic chemical precursor solutions fed into the high temperature plasma plume through a dedicated delivery device. The solvent vaporizes as the droplet travel downstream to form solid particles, and are heated & accelerated to the substrate to form finely structured coating deposits.
Key Features
The SPPS process opens up new avenues for developing compositionally complex functional oxide coatings, with the following benefits:- ability to create nanosized microstructures without any feeding problems normally associated with powder-based systems,
- flexible, rapid exploration of novel precursor compositions and their combinations
- circumvention of expensive powder feedstock preparation steps,
- better control over the chemistry of the deposit
Potential Applications
- YSZ based TBCs for gas/steam turbine applications
- Pure ï¡-Al2O3 based dielectric coatings
- Graphene films for wear resistance, energy storage applications
- LSM, LiFePO4, etc for electrodes (anode & cathode) of SOFCs/Li-Ion Batteries
- Ferrites and Titania for photocatalytic applications
- Solar absorption coatings
Intellectual Property Development Indices (IPDI) 
- Developed wide ranging functional coatings for diverse industrial applications
- Prototype demonstration of various coatings is in progress
Status | 1 | 2 | 3 | 4 | 5 | 6 | 7 | 8 | 9 | 10 |
Major Patents / Publications
Major Patents
Major Publications
- Easwaramoorthi Ramasamy, Sivakumar Govindarajan, Shrikant Joshi, Production of Graphene based Materials by Thermal Spray, ARCI patent appln. no. 2626/DEL/2015
- G. Sivakumar, R.O. Dusane, and S.V. Joshi, “Understanding the Formation of Vertical cracks in Solution Precursor Plasma Sprayed Yttria-Stabilized-Zirconia Coatings”, Journal of American Ceramic Society, 97(11), 3396-3406, 2014
- G. Sivakumar, Rajiv O. Dusane and Shrikant V. Joshi, A novel approach to process phase pure ï¡-Al2O3 coatings by solution precursor plasma spraying’, Journal of the European Ceramic Society, 33 (2013) 2823–2829
Repair and Refurbishment of Pressure Die Casting Die Components using Laser Material Deposition (Laser Cladding)
Overview
Enhancing service life by surface treatment and recovering component after post damage could have significant economic benefits. Die tool costs 10% of cast part. Repair and refurbishment are increasingly common practices, seeking to maximize unit lifetime, availability and profitability.
Key Features
- Repair is possible without preheating of the components/tools
- Low heat input to the component, so less damage
- Narrow soft zone created with relatively high hardness
- Fully automated and repeatable
- Precise deposition and less post processing
Potential Applications
- Pressure die casting tools
- High Temperature Extrusion tools
- Hot Forging tools
- Hot forming and Punching tools
Intellectual Property Development Indices (IPDI) 
- Successfully completed testing of repaired PDC tools on real-time conditions (Case study)
Status | 1 | 2 | 3 | 4 | 5 | 6 | 7 | 8 | 9 | 10 |
Thermally and microwave-irradiated exfoliated graphite for oil spill remediation
Overview
Every year with new events of oil spills has increased the need of finding a solution for this worldwide issue. This causes excess amounts of loss of oil, aquatic habitats, loss of gallons of water, and economic resources too. With daily achievement of new materials for oil remediation dispersants, absorbents, solidifiers, booms and skimmers in the market, exfoliated graphite has been found to be the best oil absorbent in oil spill absorption and recovery. This kind of materials shows porosity and ability to absorb oil in the presence of water selectively. Heavy oils sorption into the exfoliated graphite could be recovered either by a simple compression or suction filtration with a recovery ratio of 60–80 %. The bulk density of exfoliated graphite (EG) and viscosity of oil are the major influencing factors on absorption kinetic characteristics. The EG with the bulk density of 10 kg/m3 has a little less sorption capacity (about 70 g/g). Various types of oils (Hydraulic, Engine, Diesel, Shell SAE 90, Shell SAE 140, and Transformer Oil) with different viscosity were tested in order to know the amount of sorption happening over exfoliated graphite.
Key Features
- Highly porous with very less density
- Nearly 300 % expansion
- Selectively absorb oil in oil-water mixture
- Hydrophobic in nature
- Binder-free compaction
- Continuous bulk production
Potential Applications
- Oil remediation
- Nano grease
- Oil based thermally conductive ink
- Nanolubrication
Intellectual Property Development Indices (IPDI) 
- Oil absorption is validated at laboratory scale
- Continuous production of exfoliated graphite
- Oil absorption unit is established for demonstration
Status | 1 | 2 | 3 | 4 | 5 | 6 | 7 | 8 | 9 | 10 |
Reclamation of Turbo Shaft by Laser Clad Coating
Overview
Heavy engineering industries use various big and expensive components like Turbo shaft. A localize wear or other damage on a critical location can lead to scrapping the entire component. A turbo shaft is such component which gets wear on the bearing seat area. Refurbishment was done by removing the damaged layer and rebuilding a new clad layer using laser clad deposition method. A Cobalt based powder was chosen for the refurbishment to improve the wear properties and enhance the life of the refurbished component. Defect-free coating of 1.8 mm thickness across the contour of seating area was produced by diode laser cladding with following characteristics:
- UT-defect free
- ~ 0.6 mm finish grinding allowance
- ~ 0.6% porosity
- Micro-hardness 500-550 HV
- Dilution of base metal into clad ~ 8%.
Key Features
- Negligible porosity
- Controlled heat input
- Minimal heat affected region
- Precise and controlled process
- No distortion
Potential Applications
- Turbo shafts
- Steam turbine and gas turbines
Intellectual Property Development Indices (IPDI) 
- Refurbished shaft was used by end user and demonstrated excellent performance
Status | 1 | 2 | 3 | 4 | 5 | 6 | 7 | 8 | 9 | 10 |
Life Enhancement of Thermal Power Plant Components by Laser Cladding
Overview
In power plants, degradation of various components like coal nozzle tips, boiler tubes, burner spreaders, etc, due to various modes of wear, erosion and corrosion, is a common problem leading to their replacement during maintenance schedules. Such tribological systems, working in high temperature aggressive environments, require suitable surface modification solutions for life enhancement.
Key Features
- Highly controlled process
- Flexibility to adopt the process for different components
- Selective clad coating where needed
- Excellent metallurgical bond between coating and surface
- No post clad heat treatment required
Potential Applications
- Baffle plates
- Boiler tube
- Burner spreaders etc
Intellectual Property Development Indices (IPDI) 
- Field trial in an actual power plant showed negligible wear after 15 month of service
Status | 1 | 2 | 3 | 4 | 5 | 6 | 7 | 8 | 9 | 10 |
Major Patents / Publications
Major Publications
- “A novel method of pulsed laser cladding for effective control of melting of WC particulates in NiCr-WC composite coatings” Manish Tak, SM Shariff, Vikram Sake, G Padmanabham, Proceedings of 31st International Congress of Laser & Electro optic (ICALEO), p515-523, 2012
- “Characteristics and erosive wear performance of Ni-Cr based coatings on SS-310 steel by diode laser cladding and weldoverlay processes”, Proceeding of International conference on Surface Modification Technologies (SMT-23)
Laser Hardening of Hemming Beds
Overview
Hemming beds or forming dies are widely used in the automotive industry. The edges which are used for forming are subjected to high wear and require hardening to improve the bed’s life. Laser hardening provide an excellent control on the energy input enabling hardening of cast iron without melting. The surface temperature regulation system available at ARCI provides added control while processing 3D contours as well negligible change in the surface finish can eliminate the requirement of any post hardening machining.
Key Features
- Selective and localised hardening process
- No coolant or quenching medium required
- Uniform hardened layer throughout the processed area
- Negligible change in the surface roughness
- Compressive stresses in the hardened region
- Automation possible, No human errors
- Case depth 0.8 - 1.2 mm with ~55HRc uniform hardness throughout the bed Material (GGG70L Nodular Cast Iron)
Potential Applications
- Hemming beds and Forming dies made of cast iron and steels
Intellectual Property Development Indices (IPDI) 
- Laser hardened hemming beds were used by end user with excellent performance compared to flame hardened beds
Status | 1 | 2 | 3 | 4 | 5 | 6 | 7 | 8 | 9 | 10 |
Laser Assisted Machining for AUSC Boiler
Overview
The proposed AUSC boiler will have IN617 and IN625 parts / components in very high volume. However, nickel-based alloys are known as difficult-to-machine materials due to high strength and low thermal conductivity that make the cutting forces and cutting temperature very high leading to a short tool life. Hence, machining cost of these parts will be very high. Laser Assisted Machining (LAM), the material is locally heated and softened by an intense laser source prior to material removal, without melting or sublimation of the work piece as depicted in fig. This enables the difficult-to-machine materials to be machined more easily and with low machine power consumption, which leads to increase in material removal rate and productivity.
Key Features
- Softening of the material by heating
- Reduction in tool forces
- Better finish
- Lower tool wear
Potential Applications
- Component made of hard to machine alloys
- Ni based super alloys, Ti-based alloys, ceramics
Intellectual Property Development Indices (IPDI) 
- Performance and stability are validated at laboratory scale
- Scale-up and prototype module fabrication underway(Arial Narrow 10 pt – Not more than 3 bullet points of one line)
Status | 1 | 2 | 3 | 4 | 5 | 6 | 7 | 8 | 9 | 10 |
Major Patents / Publications
Major Patents
Major Publications
Laser Hardening of Crank Shafts
Overview
Crankshaft is one of the critical parts in an automotive engine, generally made of medium carbon steel requiring good wear resistance at contact areas (at bearings contact region and pin area) coupled with high load-bearing capacity. Laser surface transformation hardening process provides excellent surface finish with elimination of post-process machining requirement, no part distortion and easy adaptation to any dimension. Excellent control on the energy input leads to a uniform hardened layer across the component. A two-wheeler air-compressor crankshaft made of En18D material was successful;ly laser hardened and field trialled. Hardness in the range of 500 – 650 HV with a uniform case depth of about 300 μm was achieved. Net residual stress in the treated layer was ~ -310 MPa with 2-3% retained austenite. Laser hardened crankshafts showed 30% more life in field trials
Key Features
- Selective and localised hardening process
- No coolant or quenching medium required
- Uniform hardened layer throughout the processed area
- Negligible change in the surface roughness
- Compressive stresses in the hardened region
- Automation possible
Potential Applications
- Crank shafts
- Cam shafts
- Gears
Intellectual Property Development Indices (IPDI) 
- Laser hardened crank shafts showed 30% more life in field trials
Status | 1 | 2 | 3 | 4 | 5 | 6 | 7 | 8 | 9 | 10 |
Major Patents / Publications
Major Patents
Major Publications
- Laser Surface Hardening of Crankshafts, SAE 2009-28-0053
Refurbishment of components made of High Tensile Steel
Overview
High tensile steels are commonly used in aerospace, automotive, energy and general engineering sectors for various power transmission gears shafts, connecting rods propeller shafts, and heavy forgings such as rotors, shafts, disc etc. Such components can be damaged during operation due to wear at the contact areas and refurbishment of such components using laser cladding can save the replacement cost. Also, refurbishment technology can be beneficial in countering environmental concerns. Refurbishment technology using laser cladding for one of such component was developed that faces wear during operation due to relative movement between the contact surfaces. A post heat treatment was developed that can homogenise the clad and HAZ microstructure without creating dimensional and microstructural variation in the component. Microstructural, mechanical, and wear properties were found on par with the substrate. Component successfully completed the simulated field trial
Key Features
- Negligible porosity
- Controlled heat input
- Minimal heat affected region
- Precise and controlled process
- Special post heat treatment for improved properties
Potential Applications
- Pinion housing of Helicopters
- Components made of high tensile steels
Intellectual Property Development Indices (IPDI) 
Status | 1 | 2 | 3 | 4 | 5 | 6 | 7 | 8 | 9 | 10 |
Major Patents / Publications
Major Patents
- A patent is filed
Major Publications
High Power Impulse Magnetron Sputtering (HiPIMS) facility
Overview
Magnetron sputtering is one of the well-known Physical Vapor Deposition (PVD) technique for generating defect-free thin films at low deposition temperatures. Contrary to any other PVD techniques, magnetron sputtering is a process in which the removal of the target material (in other words like evaporation) takes place through the momentum transfer process. Since it is a momentum transfer process, literally using this technique, most of the materials deposition can be done. In similar lines, High Power Impulse Magnetron Sputtering (HiPIMS) is a process in which, the power given to the source/target will be in short pulses of very high energy. In general, the high energy ionic depositions are known for achieving good adhesion, high density and good control over reactive process. As on date, the HiPIMS facility at ARCI is a lab scale equipment with planar as well as cylindrical cathodes. The HiPIMS facility with its unique advantages can be used for developing thin films that are key to major sectors like, automobile, aerospace, manufacturing, optics, electronics, alternate energy, biomedical, sensors, etc.
Key Features
- The facility can be used to deposit any metallic or reactive depositions (Metals, Metal nitrides, metal oxides & metal carbides)
- Can be used to develop thin films on internal or external surfaces of any regular objects
Potential Applications
- Any metallic, nitride or oxide coatings can be deposited
- Solar selective coatings for solar thermal applications
- Diffusion barrier coatings for electronic components
- Decorative coatings for aesthetic applications
- Biocompatible coatings for biomedical applications
- Coatings for developing different sensors
Intellectual Property Development Indices (IPDI) 
Status | 1 | 2 | 3 | 4 | 5 | 6 | 7 | 8 | 9 | 10 |
Major Patents / Publications
Major Patents
Major Publications
- Patent: “Improved cylindrical magnetron cathode and a process for depositing thin films on surfaces using the said cathode” application No. 21/DEL/2008, January 3 2008.
Visible and Sunlight Photocatalytic Active Self-Cleaning Technology
Overview
Titanium dioxide (TiO2), the most promising photocatalytic material is already used in various practical applications, such as sterilization, deodorization, self-cleaning and super hydrophilic functionality by the strong oxidizing agents (holes and free radicals) thereof being generated after exposure to light. Conventional TiO2 materials most preferably prepared from sol-gel, and other conventional methods can active (generating oxidizing species) only under the exposure to UV lights because of its large band gap of 3.20 eV. Moreover, if a conventional TiO2 material is illuminated with visible light (>400nm), oxidizing species cannot be formed because of no charge carrier formation. To activate in the visible light, incorporation of a few weight percent of smart carbon in the form of nanoparticles or sensitized carbon either in the bulk or at the surface of titanium dioxide leads to visible-light and sunlight active suitable for indoor and outdoor self-cleaning applications. The technology of smart carbon based TiO2 nanostructure materials are available in the form of paste, suspension and thin films having highest visible and sunlight photocatalytic self-cleaning properties and they can be easily applied to any type of device/ object.
Key Features
- Highly visible and sunlight photocatalytic properties
- Good dispersion in solvents
- High stability under solar and UV light
- Easily incorporate into any type of device/object (e.g. fabrics or paints or ceramic tiles etc.)
Potential Applications
- Self-clean fabrics/ceramic tiles manufacturing
- Indoor and outdoor self-cleaning paint manufacturing
- Self-clean coatings for antibacterial and antifouling applications
Intellectual Property Development Indices (IPDI) 
- Prototype fabric has been developed and validated.
- Technology transfer are being progressed
Outcome
- A technology of smart carbon based TiO2 nanostructure materials has been successfully developed and demonstrated for indoor and outdoor self-cleaning applications
Status | 1 | 2 | 3 | 4 | 5 | 6 | 7 | 8 | 9 | 10 |
Major Patents / Publications
Major Patents
Major Publications
- Filed an Indian patent. Application No: 201811011478
High Crystalline Nanoparticles for Photovoltaic and Self-cleaning Applications
Overview
In recent years, there has been increasing interest in the application of nanoparticles in various fields because of its large effective area which enhances the surface reactions. Titanium dioxide (TiO2) & Zirconium dioxide (ZrO2) are the most important industrial materials that have been used for white pigments for a long time owing to its high refraction characteristic. Further, it is one of the main components of piezoelectric materials, dielectrics, and semi-conductors according to the development of electronic industry since it is characterized by a high dielectric constant. Still further, it has been the trend recently that its application to cosmetics, fillers, paints, lubricants, precision ceramics, anodic materials (DSSC and Perovskite, battery, etc.) functional coatings (Antireflective, corrosion protection, barrier layers, etc.) and using UV shielding and absorbance properties as well as a catalyst for removing organic contaminants according to the chemical corrosion resistance and photocatalytic effect has been extended rapidly. To view of the vast applications, the primary objective of this project work is to focus to develop highly crystalline TiO2 and ZrO2 nanoparticles along with high dispersion and uniformity suitable for the above mentioned applications.
Key Features
- High crystalline
- Uniform particle size
- Good dispersion in polar solvents
- High photocatalytic property
- Easily incorporate into any type of device/ object
Potential Applications
- Photoanodes for DSSC and Perovskite solar cells
- Self-clean fabrics/ceramic tiles and glass manufacturing
- Coatings for corrosion resistance and barrier applications
Intellectual Property Development Indices (IPDI) 
- Crystalline TiO2 and ZrO2 nanoparticles have been successfully developed by lyothermal synthesis & investigated photovoltaic and photo catalytic properties of the materials.
Outcome/Expected outcome:
- Highly dispersible crystalline nanoparticles were successfully developed & validated for solar cell and photocatalytic self-cleaning
Status | 1 | 2 | 3 | 4 | 5 | 6 | 7 | 8 | 9 | 10 |
Major Patents / Publications
Major Patents
Major Publications
Electrodeposited nanostructured NiCo2O4 based supercapacitor
Overview
With the anticipated increase in the renewable wind and solar energy supercapacitors with high specific capacitance and cycle stability have increasing demands to balance the energy storage requirements. NiCo2O4 based electrode materials with excellent electrochemical performance and high theoretical specific capacitance values serve as emerging tool for various applications like HEV’s and back-up systems. Further, electrodeposition is a cost-effective mode of synthesis both with respect to the materials employed and the equipment used. The technology aims at the synthesis of binder free electrodeposited NiCo2O4 electrode materials for supercapacitors along with the fabrication of device for practical applications
Key Features
- Cost effective synthesis strategy
- High specific capacitance (1977 F/g at 1 A/g by half cell and 91.5 F/g at 0.5 A/g by full cell)
- High power density (7.5 kW/kg at 10 A/g)
- Good capacitive retention of the ASC (74% retention for 5000 cycles)
Potential Applications
- Start-Stop systems
- HEV’s
- UPS and back-up systems
- Electronics
Intellectual Property Development Indices (IPDI) 
- ASC device performance and stability for 5000 cycles has been validated at lab scale
Status | 1 | 2 | 3 | 4 | 5 | 6 | 7 | 8 | 9 | 10 |
Major Patents / Publications
Major Patents
Major Publications
- Manuscript yet to be published
Quasi-2D perovskite solar cells
Overview
The instability of perovskite solar cells against moisture, light and heatremains the main stumbling block towards the commercialization of this technology. One of the promising strategies is to lower the dimensionality of perovskites from three-dimensional (3D) to two-dimensional (2D) which presents higher stability against the ambient environment. The conductor layers are isolated from one another by incorporating R–NH3, a large aliphatic or aromatic alkyl ammonium spacer cation. The insertion of insulating spacer cations gives 2D layered perovskites unique properties compared to their 3D counterparts. The hydrophobic nature of the organic spacer imparts 2D perovskites with superior moisture stability, these quasi2D perovskites are used as absorber layers to impart highly efficient and stable perovskite solar cells.
Key Features
- High stability towards moisture
- Tunable bandgap
Potential Applications
- Off-grid power supply
- Building integrated photovoltaics (Smart windows, roof, tiles)
- Solar road studs
Intellectual Property Development Indices (IPDI) 
Status | 1 | 2 | 3 | 4 | 5 | 6 | 7 | 8 | 9 | 10 |
Major Patents / Publications
Major Patents
Major Publications
- Patent search under process
Large area carbon based perovskite solar cells.
Overview
About 50% of the production costs of perovskite solar cells (PSCs) are accorded by the organic hole transporting materials (HTM) and the metal back contact. Using a highly conductive carbon electrode to replace both organic HTM and the metal back contact cuts down the production cost by 50%. Carbon-based materials, when used as back contacts in HTM-free PSCs, have been proved to be a class of cheap, stable, water-proof, and anticorrosive materials. By using screen printing technique large area with high uniformity and reproducible carbon based PSC can be made. As ongoing work, 100mm X 100mmcarbon based perovskite modules were developed.
Key Features
- Low material and production cost
- Highly stable perovskite devices
Potential Applications
- Off-grid power supply
- Building integrated photovoltaics (roof, tiles)
- Solar road studs
Intellectual Property Development Indices (IPDI) 
Status | 1 | 2 | 3 | 4 | 5 | 6 | 7 | 8 | 9 | 10 |
Major Patents / Publications
Major Patents
Major Publications
- Room temperature curable carbon cathode for hole-conductor free perovskite solar cells, Solar Energy, Accepted
Design, Integration and Demonstration of Super capacitor Powered and Hybrid Electric Vehicles
Overview
The concept of electric vehicle powered by Super capacitor alone as well as hybrid has been designed, integrated and demonstrated during on road conditions. To integrate the super capacitor bicycle,18 commercial SC (Maxwell) cells with individual cell specifications of 3400 F, 2.85 V and 3.85 Wh (stored energy) were procured, connected in series to obtain a module with 51.4 V and 69 Wh sufficient to run the electric motor in the bicycle. Further, the capacitor management system (CMS) has been developed to regulate the voltage and current in each cell during charge/discharge cycles. In order to extend the driving range of E-bike to 2.5 km, boost converter has been designed to boost up the voltage by recovering the remaining stored energy in SC module. Parallely, hybrid module has been developed containing 3 Lead acid batteries (12V 14Ah: 3 pack) connected in series with 3 super capacitors (2.7V, 650F, 0.66 Wh). The super capacitors aids in cranking as well during acceleration. The developed bicycles have been successfully tested during on-road conditions.
Key Features
Super capacitor powered EV:
- No. of cells in module:18 cells connected in series
- Total stored energy: 69 Wh
- Usable energy: 27.0 Wh
- Nominal voltage, V: 51.3 V
- Charging time: 4 minutes
- Driving range: 2.5 Km with booster circuit
Hybrid EV:
- Lead acid battery (36 V 14 Ah) has limitations in terms of life and power delivery
- Initial high power delivery (400 W) reduces the life time of lead acid battery
- SC (2.85 V; 650 F) provides high power (400 W) delivery for initial cranking during start and acceleration thus increasing lifespan
- On-road charging (2 Wh per charge) and peak power delivery while running
- Hybrid EV has a maximum speed of 25 kmph with motor capacity of 250 W
Potential Applications
- Automotive transport (electric bicycles, mini-bus, etc.)
Intellectual Property Development Indices (IPDI) 
- Super capacitor bicycle has been integrated and demonstrated.
- Booster circuit has been designed to extend the range of super capacitor E-bicycle
- Super capacitor module has been adopted in addition to lead acid battery pack for initial cranking and acceleration.
Status | 1 | 2 | 3 | 4 | 5 | 6 | 7 | 8 | 9 | 10 |
Major Patents / Publications
Major Patents
Major Publications
Ozone-friendly magnetic refrigerators – an alternative to conventional cooling technology for energy saving
Overview
Air conditioners and refrigeration make a major contribution to the global energy consumption. Conventional refrigerators work on energy-guzzling vapor-compression technique and they produce hydrofluorocarbons that are greenhouse gases that contribute to global climate change when they escape into the atmosphere. Thus, there is a strong thrust to develop an energy-efficient technology. Magnetic refrigeration is an environmentally friendly technology that uses magnetic fields to change a magnetic material’s temperature (i.e. the magnetocaloric effect - MCE) and allows the solid material to serve as a refrigerant. This technology is energy efficient, eco-friendly and produces low vibration and noise. Thus, the need of the hour is to find suitable magnetocaloric materials that are cost-effective and exhibit large MCE spanning over a wide temperature range from low to room temperatures. Our research aims to develop magnetocaloric materials for active magnetic refrigeration applications.
Key Features
- Developing advanced materials with magnetocaloric effect for energy efficient refrigeration.
- Rare-earth free, economic Ni-Mn based Heusler alloys, Mn- based alloys, exhibiting first-order transition are being explored for magnetic refrigeration
- A huge inverse magnetic entropy of 17 J/kg-K in Ni-Mn based Heusler alloys and 19 J/kg-K in Mn-Fe-P-Si alloy (normal magnetic entropy) are obtained near ambient temperature at 3 T magnetic field
Potential Applications
- Household refrigerators
- Air-conditioning (Halls, automobiles etc.)
- Food preservation
Intellectual Property Development Indices (IPDI) 
- Synthesized single phase and prudent Ni-Mn based and Mn based magnetocaloric materials, which exhibits magnetocaloric effect at ambient temperatures.
- Upscaling of the magnetocaloric materials is underway
- Development of prototype to demonstrate magnetic refrigeration is under progress.
Status | 1 | 2 | 3 | 4 | 5 | 6 | 7 | 8 | 9 | 10 |
Major Patents / Publications
Major Patents
Major Publications
- S.Kavita, V.V.Ramakrishna, Poonam Yadav, Sravani Kethavath, N.P.Lalla, Tiju Thomas and R.Gopalan, J.Alloys and Comp., 795,519 (2019)
High voltage carbon encapsulated-graded LiMn2O4:LiNi1-x-yCoxAlyO2 cathodes for rechargeable Li-ion pouch cells
Overview
Layered-structures such as LiNi1-x-yMnxCoyO2 and LiNi1-x-yCoxAlyO2 are currently used as cathode materials in LIB for high-energy applications. However, practical achievable capacity of these materials are restricted to 150-200 mAh/g due to the limitation in the achievable charging voltage (4.2 V) with acceptable cyclic stability. If over-charge (above 4.2 V) induced surface degradation in LiNi1-x-yCoxAlyO2 can be prevented, it is possible to achieve high reversible capacity up to 230 to 250 mAh/g. The minimization of surface induced degradation is observed in surface modified LiNi1-x-yCoxAlyO2 (LNCA)
Key Features
- Scalable synthesis method
- Higher specific capacity
Potential Applications
- Lithium ion batteries
Funding Agency : DST
Intellectual Property Development Indices (IPDI) 
Status | 1 | 2 | 3 | 4 | 5 | 6 | 7 | 8 | 9 | 10 |
Major Patents / Publications
Major Patents
Major Publications
- Concentration Gradient-Driven Aluminum Diffusion in a Single-Step Coprecipitation of a Compositionally Graded Precursor for LiNi0.8Co0.135Al0.065O2 with Mitigated Irreversibility of H2 ↔ H3 Phase Transition, Sasikala Natarajan, Sahana B. Moodakare, Prathap Haridoss and Raghavan Gopalan, ACS Appl. Mater. Interfaces 2020, 12, 31, 34959–34970
Low-cost Sodium ion batteries for energy storage applications
Overview
Sodium ion batteries (SIBs) are considered as potential alternative to Lithium ion batteries (LIBs) for large scale energy storage applications, such as grid energy storage and electric vehicle (EV) applications due to abundance of sodium, high specific energy and low-cost. However, plenty of research efforts are required to find suitable electrodes and electrolytes to achieve specific energy similar to that of LIBs. Hence, different electrode materials are selected based on their promising electrochemical performances. Polyanionic compounds with long cycle life and layered sodium transition metal oxides with high specific capacity as cathodes; whereas hard carbon and sodium titanates with low sodium insertion potential and high specific capacity as anodes have been prepared using novel chemical approaches and their electrochemical performances have been investigated using indigenously developed non-aqueous based electrolyte. Full cells (Pouch-type) have been fabricated using polyanionic compound (here, sodium vanadium phosphate) as cathode and hard carbon as anode and the electrochemical studies are under progress.
Key Features
- High specific energy and power density, good rate capability, excellent cycle life, high thermal stability and safe-in operation.
- Low- cost and wider operating temperature range.
Potential Applications
- Large scale electric energy storage (EES)
- Stationary energy storage
- Electric/hybrid electric vehicles
Intellectual Property Development Indices (IPDI) 
- Electrolytes with high ionic conductivity (>10-3 S/cm) and electrochemical stability window (>4.2 V) has been prepared and tested.
- Electrode materials with excellent sodium ion storage performance has been developed, where cycle life >1000 cycles has been demonstrated in full cell configuration.
- Optimization of large scale synthesis (500 g/batch) and pouch cell fabrication (1 Ah) are under progress.
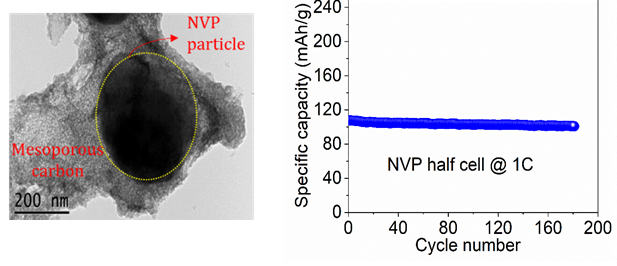
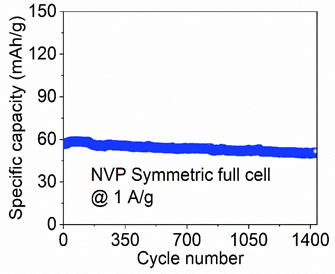
Status | 1 | 2 | 3 | 4 | 5 | 6 | 7 | 8 | 9 | 10 |
Major Patents / Publications
Major Patents
- Microwave assisted sol-gel process for preparing in-situ carbon coated electrode materials and the product there of,” (2019) Bijoy Kumar Das, P. Laxman Manikanta, N. Lakshmipriya, R. Gopalan, G. Sundararajan, Indian Patent 201911008004.
- Microwave assisted sol-gel process for preparing in-situ carbon coated electrode materials and the product thereof”, (2020) Bijoy Kumar Das, P. Laxman Manikanta, N. Lakshmipriya, R. Gopalan, G. Sundararajan, European Patent: 20763813.1
- Microwave assisted sol-gel process for preparing in-situ carbon coated electrode materials and the product thereof”, (2020) Bijoy Kumar Das, P. Laxman Manikanta, N. Lakshmipriya, R. Gopalan, G. Sundararajan, Japanese Patent: 2020-550159
- Microwave assisted sol-gel process for preparing in-situ carbon coated electrode materials and the product thereof”, (2020) Bijoy Kumar Das, P. Laxman Manikanta, N. Lakshmipriya, R. Gopalan, G. Sundararajan, Korean Patent: 10-2020-7025994
Major Publications
- Scalable synthesis and kinetic studies of carbon coated sodium titanate: A promising ultra-low intercalation voltage anode for sodium ion battery”, P. Laxman Mani Kanta, M. Venktesh, Satyesh Kumar Yadav, Bijoy Kumar Das*, R. Gopalan, Trans. Ind. Nation. Acad. Eng. 5 (2020) 475-483.
Book Chapter
- Bijoy Kumar Das, R. Gopalan (2019) 'Intercalation-based Layered Materials for Rechargeable Sodium-ion Batteries', Layered Materials for Energy Storage and Conversion. RSC Publisher.
Tungsten- based plates by spark plasma sintering
Overview
Tungsten based structural components are commercially being prepared from wrought tungsten by hot-pressing/sintering followed by hot rolling at high temperatures. An alternate simple PM processing route comprising of blending, milling, reduction and spark plasma sintering could be adopted for fabricating such components. The advantage of such processing is retention of fine grain size with uniform distribution and no abnormal grain growth leading to improved hardness and strength in the sintered components. The role of additives was found to be critical in achieving properties identical to that of hot rolled components. The powder composition and the processing conditions was optimized. Microstructural investigations through SEM and EBSD were carried out to explain the enhanced densification at much lower temperatures and were correlated with the mechanical properties achieved.
Key Features
- Fabricated in sizes of 20, 50 and 95 mm diameter upto 10 mm thickness
- Density 98.5% of theoretical with grain size 2-3 µm
- Hardness > 450 HVN and TRS ≥ 750 MPa achieved
- Additives play an important role in attaining properties
- Milling, reduction and sintering steps are involved
- Scaled up process for commercial applications
- Alternate PM based route for fabricating W-components
Potential Applications
- Strategic applications
Intellectual Property Development Indices (IPDI) 
- Processing and properties are validated at laboratory scale
- Coupon level demonstrated
- Scaled up technology available
Status | 1 | 2 | 3 | 4 | 5 | 6 | 7 | 8 | 9 | 10 |
Major Patents / Publications
Major Patents
Major Publications
- Dibyendu Chakravarty, PVV Srinivas and R. Vijay, ‘Method of fabricating tungsten based composite sheets by spark plasma sintering technique for making components’, Indian Patent application no. 201911014933, dtd. 13.04.2019
- Ultrahigh transverse rupture strength in tungsten-based nanocomposites with minimal lattice misfit and dual microstructure, Int. J. Ref. Metals New Mater. 95, 105454, 2021.
Electrochemical Methanol Reformation (ECMR) for Hydrogen Generation
Overview
Key Features
Potential Applications
Intellectual Property Development Indices (IPDI) 
Status | 1 | 2 | 3 | 4 | 5 | 6 | 7 | 8 | 9 | 10 |
Major Patents / Publications
Major Patents
Major Publications
Setting up of Automated PEM Fuel Cell component/stack assembly Line
Overview
Key Features
- Development of automated pilot line with Indian collaborator to realise indigeneious development.
- Development of PEMFC stacks with more indigeneious components.
- Establishment of this facility is first of its kind in India.
- Provide simplification for mass manufacture of components/stack
Potential Applications
Intellectual Property Development Indices (IPDI) 
Status | 1 | 2 | 3 | 4 | 5 | 6 | 7 | 8 | 9 | 10 |
Major Patents / Publications
Major Patents
Major Publications
Porous alumina-polymer beads for toxic fluoride removal from drinking water
Overview
Excess fluoride level in ground water used for drinking is causing serious health problems in several states of India. The permissible limit of fluoride in drinking water, as per WHO, is 1 ppm. The fluoride content is found to be in the range of 2 to 20 ppm in different regions of India. The processes like reverse osmosis, ion exchange, etc., used for removal of fluoride require special equipment and periodic maintenance and is not affordable to all. There is a necessity for a “point-of-use” device for instant removal of fluoride from drinking water specially for travellers, pregnant women and school children. Alumina in the form of bohemite structure is known to be the best fluoride adsorption material. ARCI has developed alumina-polymer cross-linked beads with high porosity for removal of fluoride from water. A porous structure having high surface area increases the contact volume of water thereby improving the removal rate and efficiency. The polymer crosslinking arrests the leaching of alumina in to water.
Key Features
- Simple process
- Bead size: 1-2 mm, spherical
- Surface area: 240 m2/g
- Mesoporous
- Primary particle size: 10-30 nm
- Chemical composition: Bohemite corsslinked polymer
- Can remove 10 ppm fluoride from water in 2-30 mins depending on the volume
Potential Applications
- Toxic fluoride removal for safe drinking water
Technology Readiness Level (TRL):
- Processing and properties are validated at laboratory scale
- Coupon level demonstrated
- Field trials on lab prototype are in progress
Intellectual Property Development Indices (IPDI) 
- Basic concepts and understanding of underlying scientific principles
- Short listing possible applications
- Research to prove technical feasibility for targeted application
- Coupon level testing in stimulated conditions
- Check repeatability/ consistency at coupon level
Status | 1 | 2 | 3 | 4 | 5 | 6 | 7 | 8 | 9 | 10 |
Major Patents / Publications
Major Patents
Major Publications
Cathodic Arc Physical Vapor Deposition Facility (CAPVD)
Overview
In general, Cathodic Arc PVD is a three step process: (i) Vaporization of required material from a source (cathode) by using an electric arc, (ii) Transport of vaporized material to the destination (target to be coated) and (iii) Condensation of transported vapours on to the targeted object to make a thin film. The major advantages of the CAPVD include; formation of highly dense and adherent coatings with a good deposition rate and thickness control (± 5 nm). The semi industrial available facility at ARCI is associated with 400 mm length (Ф: 110 mm) cylindrical cathodes which enable reduced droplets formation than any other conventional CAPVD facilities. The maximum dimensions of the target to be coated can be: 350 mm L x 100 mm W (Ф). The CAPVD facility with its unique advantages can be used for developing thin films/ coatings in major sectors like; auto mobile, aerospace, manufacturing, optics, electronics, alternate energy, etc.
Key Features
- Films/coatings of different structures with good control over chemistry and thickness can be developed: (i). Mono-layer, (ii) Multi-layer, (iii) Gradient and (iv) Functionally multi-layered/graded
- Films/coatings containing Ti, Cr, AlSi & AlTi can be coated in pure metallic or nitride or carbide form. i.e. TiN, CrN, TiAlN, TiAlSiN, CrAlSiN, TiCrAlSiN, TiC, TiCN, TiAlCN, etc.
- Physical and mechanical properties can be tuned by varying deposition conditions
- Environmentally green and easily up scalable process with high production rates
Potential Applications
- Hard and wear resistant coatings for cutting tools – up to hardness of 45 GPa
- - High speed and dry machining
- - Machining of advanced materials: CGI, Ti6Al4V, Inconel 718, etc.
- Wear resistant coatings for dies, bearings, etc. – Low friction coefficient of < 0.2
- Erosion resistant coatings for compressor blades – A thickness of 20 μm is achieved
- Solar selective coatings for solar thermal applications – ~ α: 0.96 & ε: 0.09 at 400°C
- Diffusion barrier coatings for electronic components
- Decorative coatings for aesthetic applications, etc.
Intellectual Property Development Indices (IPDI) 
- Different nanocomposite hard coatings were developed and tested for their performance
- 20 μm thick TiCrN erosion resistant coating developed
- TiCrCN wear resistant coatings were demonstrated for die applications
- Cr/TiCrAlN/TiAlN/AlSiN/AlSiO solar selective coatings were demonstrated on 75 mm diameter SS tubes (~ α: 0.96 & ε: 0.09 at 400°C)
Status | 1 | 2 | 3 | 4 | 5 | 6 | 7 | 8 | 9 | 10 |
Major Patents / Publications
Major Publications
- “An improved solar selective multi-layer coating and a method of depositing the same” Application No. 1567/DEL/2012, May 22nd 2012.
- "Studies on cathodic arc PVD grown TiCrN based erosion resistant thin films" Krishna Valleti, Puneet C, Rama Krishna L, and Shrikant V. Joshi, JVST A 34, (2016): 041512
- “High temperature stable solar selective coatings by cathodic arc PVD for heat collecting elements” Krishna Valleti, D. Murali Krishna, P. Mohan Reddy, Shrikant V. Joshi, Solar Energy Materials and Solar Cells 145 (2016):447
High Performance Broad Band Antireflective Coatings
Overview
The constantly growing demand for optoelectronic and optical equipment in diverse areas, including consumer electronics and space exploration has created the need to identify the best ways to improve the efficiency of light collection. In this regard, development of broad-band anti-reflective coatings (BARCs) has attracted substantial research interest due to their high transmittance in a broad wavelength range (300–2500 nm). Due to their high refractive indices, optical elements like glass and polymeric transparent substrates suffer a reflection loss of about 8-9% in the visible spectrum of the solar radiation. Such reflection losses are undesirable and detrimental to the overall light to electricity conversion efficiency. Hence, BARCs that transfer maximum incident light over a broad range of wavelengths can help to achieve competitive conversion efficiencies in solar cells
Key Features
- High transmittances in visible and solar regions: >98 % (in visible) >96% (in solar)
- Low temperature curable (80-1000C)
- High temperature stability: Max up to 10000C
- Weather stability: > 200hrs withstand in high humidity (>90%) at 500C
- High mechanical stability and Long durability
- Coat effective coating technique
Potential Applications
- Solar PV & CSP cover glass
- Optical lenses
- Video display panels
- Architectural glasses
- High power lasers
Intellectual Property Development Indices (IPDI) 
Status | 1 | 2 | 3 | 4 | 5 | 6 | 7 | 8 | 9 | 10 |
Major Patents / Publications
Major Patents
- Indian patent Application no. 4041/DEL/2014, date of filling: 31.12.14.
- High Performance and Environmentally Stable Broad Band Antireflective Coatings using Novel Ink-Bottle Mesoporous MgF2 Nanoparticles for Solar Applications, Solar Energy Materials & Solar Cells 159 (2017) 204–211.
Major Publications
Cold Gas Dynamic Spray Technology
Overview
Cold gas dynamic spray (also called Cold Spray or Kinetic Spray) involves accelerating micron sized powder particles to supersonic velocities resulting in the formation of dense, thick and pure coatings with high deposiotion rates. Cold spray is a low temperature high velocity variant of thermal spray family. This technique has very high deposition rates and deposition efficiencies. Since there is no heating of powders, retention of powder properties in the coating is possible. Dense coatings with porosity less than 0.1% can be achieved. Metallic, Alloy, Composites, Nanostructured and Amorphous powders can be deposited. This technology has huge potential for repair and refurbishment, electrical and thermal applications.
Key Features
- Indigenously developed state of the art PLC based automated Portable control panel (Max Pressure – 20 bar)
- Different set of nozzles
- For Low melting materials (polymer based)
- High deposition rate or coverage area
- Low deposition rate or coverage area
- For Ni based materials, Steels (Optional)
- Compressed AIR as process and carrier gas
- Maximum Pressure- 20 bar; Maximum Temperature-600oC
- Cu, Al, Ag, Zn, Sn,Ni, SS, Ta, Nb, Ti and alloys and composites
Potential Applications
- Repair and Refurbishment Applications ( Aerospace components such as Compressor Fan casing etc.,)
- Coatings for Electrical contacts, lugs, EMI shielding, heat sinks
- Coatings for High Temp Corrosion resistance, Bio medical, Sputter Target
- Sacrificial coatings or Cathodic Protection (Zinc coating on Steel Strcutures)
- Anodic Protection coatings (Aluminium coatings on Active Magnesium aerospace and automotive components)
- Wear resistant coatings ( MMCs, Alloy coatings)
- Nanostrcutured / amorpohous/ BMG coatings
- High Entropy Alloy Coatings as Bondcoats for High Temperature Gas Turbine Applications
Intellectual Property Development Indices (IPDI) 
- Technology Ready for Adaptation
- Application Development Activities in progress
Status | 1 | 2 | 3 | 4 | 5 | 6 | 7 | 8 | 9 | 10 |
Major Patents / Publications
Major Publications
- Naveen M Chavan, SP Phani, M Ramakrishna, DS Rao and G Sundararajan, Surface & Coatings Technology 205 (2011), P4798–4807
- G Sundararajan, Naveen M Chavan and S Kumar, Journal of Thermal Spray Technology, 1348—Volume 22(8) December 2013
- S Kumar, A.Jyothirmayi, Nitin Wasekar and SV Joshi, Surface and Coatings Technology, 296(2016), 124-135
Pulsed Electrodeposition Technology
Overview
Pulsed Electrodeposition is a unique non-line-of-sight electrolytic deposition technique for obtaining wear and corrosion resistant nanocrystalline coatings using modulated currents. The process utilizes non hazardous electrolyte and pulsed current to achieve desired microstructure and mechanical properties in hardness gradient nanocrystalline Nickel, Sacrificial Zn, Nanocrystalline alloys of Ni-P, Ni-W, Ni-Mo, Fe-W coatings. The technology is explored for grain boundary engineering resulting in control over grain size from 200 nm to 3 nm. Recently a new method is invented to deposit nanocomposite coatings for hard chrome replacement with control over inert particle content in coating depending upon application requirement. The new nanocomposite demonstrated excellent wear and corrosion resistance in comparison with hard chrome and commercial NIKASIL coatings. The process is economical and effortlessly scalable to existing electroplating industry with low initial capital investment.
Key Features
- Non line of site process, economical and ecofriendly
- Porosity free finished product, higher production rates
- Control over microstructure, mechanical properties, particle content in composite coating
- Higher current efficiency and deposition rates compared to traditional hard chrome process
- Easy technology transfer from research lab to existing infrastructure
Potential Applications
- Corrosion resistance and decorative coatings: automobiles include car, truck trim, motorcycle, kitchen and bathroom appliances
- Wear resistance: hydraulic actuators, railway engine shafts, aircraft landing gears, shaft journals, farm machinery, earth movers, snow plows, road repair equipment, mining equipment, automobile engine valves
- Industrial tools such as rolls for Al and steel manufacturing, stamping tools and dies, molds for plastic manufacturing utilized chrome plating for increasing its (tool) life
Intellectual Property Development Indices (IPDI) 
- Performance and stability are validated at laboratory and industry scale
- Scale-up version is also available up to 500 cm2 for industrial component
Status | 1 | 2 | 3 | 4 | 5 | 6 | 7 | 8 | 9 | 10 |
Major Patents / Publications
Major Publications
- An improved method for preparing nickel electrodeposit having predetermined hardness gradient (Indian Patent: IN200901455-I1)
- A method and an apparatus for preparing nickel tungsten based nanocomposite coating deposition (Indian Patent: 201611001190)
- Nitin P. Wasekar et al., Materials and Design, 112 (2016) pp. 140-150, Applied Surface Science, 364 (2016), pp. 264-272, Surface and Coatings Technology, 291 (2016) pp. 130-140, Materials Characterization, 116 (2016) pp. 1-7, Wear 342 (2015) pp. 340-348.
Hybrid Precursor Powder Plasma Spray Technology
Overview
Hybrid processing involves depositing layered or composite coating architecture using sequential or simultaneous feeding of powder and liquid feedstock, respectively. Independently controlled micron sized powder feedstock and liquid precursor solution are fed into the plasma spray plume to form the desired coatings. The concept is extremely convenient to adopt, as it involves only a minor modification in the injection arrangement in any existing thermal spray facility.
Key Features
The concept of hybrid processing opens up possibilities for depositing coatings with diverse architecture- Layered coatings by sequential feeding of liquid and powder feedstock
- Composite coatings by simultaneous feeding of liquid and powder feedstock
- Graded coatings by simultaneous feeding of liquid and powder feedstock, while continuously varying the feed rates of one or both feedstock.
Potential Applications
- Composite YSZ based TBCs for gas/steam turbine applications
- Composite alloy/metallic + ceramic coatings for wear resistance
- Oxide dispersed coatings for elevated temperature applications
Intellectual Property Development Indices (IPDI) 
- Developed wide ranging functional coatings for diverse industrial applications
- Prototype demonstration of various coatings is in progress
Status | 1 | 2 | 3 | 4 | 5 | 6 | 7 | 8 | 9 | 10 |
Major Patents / Publications
Major Publications
- G. Sivakumar and S.V. Joshi, ‘An improved hybrid methodology for producing composite, multi-layered and graded coatings by plasma spraying utilizing powder and solution precursor feedstock’, Indian Pat. No. 2965/DEL/2011 dt. 17th Oct, 2011
- A. Lohia, G. Sivakumar, M. Ramakrishna and S.V. Joshi, “Deposition of Nanocomposite Coatings employing a Hybrid APS + SPPS Technique”, Journal of Thermal Spray Technology, 23(7), 1054-1064, 2014
- S.V. Joshi and G. Sivakumar, Hybrid processing with powders and solutions: A novel approach to deposit composite coatings, Journal of Thermal Spray Technology, 24 (7), pp. 1166-1186, 2015
Micro Arc Oxidation Coating Technology
Overview
Micro Arc Oxidation (MAO) also known as Plasma Electrolytic Oxidation (PEO) is a novel and environmental friendly way of creating dense, ultra-hard (peak hardness up to 1800 HV) ceramic composite coatings for enhancing the wear, corrosion, electrical and thermal protection of Al alloys. MAO is an electro-chemical and electro-thermal oxidation in an alkaline electrolyte and the surface oxidation is driven by the supply of high voltage (up to 600 V) pulsed AC power. MAO coatings deposited on a large variety Al alloys such as 3-times harder, 15 times wear resistant and 10 times corrosion resistant than the hard anodized layers. Further, MAO technology can treat the difficult to anodize class of alloys such as Al-Si cast products. Through rigorous R&D activities pursued over last 2 decades, ARCI has mastered over the MAO process including the equipment design, building, testing, supply, installation and commissioning of academic scale, lab scale and industry scale systems with custom built capacities and capabilities.
Key Features
- Custom-built technology systems are available in large power supply ranges between 20 to 500 kVA depending upon the scale of operations
- Apart from a variety of Al alloys, coatings can also be formed on metallic components made out of Mg, Ti, Zr and their alloys
- It is possible to engineer the coating composition through additives added to the electrolyte depending upon the functional requirements of various industrial components
- Coating hardness increases with increasing thickness due to concurrently increased alpha alumina phase in the coating structure
Potential Applications
- Taking advantage of enhanced fatigue strength in addition to the wear, corrosion, thermal and electrical protection, numerous applications ranging from automotive, aerospace, wire drawing and textile industry are the potential segments
- Although the MAO process is discrete, continuous coating deposition technology developed on the basic platform of MAO coating formation is useful for providing an insulating coating on foils and wires of kilometre long is useful for electrical and electronics application.
Intellectual Property Development Indices (IPDI) 
- Prototype models of academic and industry scale systems were already fabricated, tested and demonstrated on a variety of applications, installed at customer locations.
- Application development for various industry segments is currently in progress to promote more technology transfers to the Indian industries and universities.
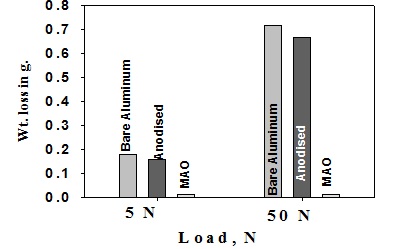
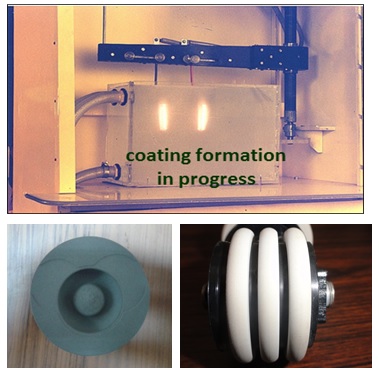
Status | 1 | 2 | 3 | 4 | 5 | 6 | 7 | 8 | 9 | 10 |
Major Patents / Publications
Major Patents
- Indian Patent Applications: (a) 209817, (b) 1828/DEL/2008/01082008, (c) 1839/DEL/2015, US Patent Applications: (d) 6,893,551, (e) 8,486,237, (f) 9,365,945 UK Patent Application: (g) GB2464378, Japan Patent No: (h) 5442386, German Patent No: (i) 10 2009 044 256, French Patent Application: (j) 0957102, Brazil Patent No: (k) Pl0904232-6 A2 and South Africa Patent No: (l) ZA200906786.
Major Publications
- L. Rama Krishna et. al., Surface and Coatings Technology, vol. 163-164, 2003, pp. 484-490, Wear, vol. 261, 2006, pp. 1095-1101, Surface and Coatings Technology, vol. 167, 2003, pp. 269-277.
- L. Rama Krishna et. al., Metallurgical and Materials Transactions A, vol. 38, 2007, pp. 370-378, Surface and Coatings Technology, vol. 269, 2015, pp. 54-63, Journal of Alloys and Compounds, vol. 578, 2013, pp. 355-361.
Advanced Detonation Spray Coating Technology (DSC) MARK-II
Overview
With an overall objective of enhancing the efficiency, productivity and reliability by increasing the detonation frequency (more than 3Hz) of the existing DSC system, design of various critical parts and its integration with the existing system has been initiated. Accordingly, one DSC advanced system has already been fabricated and subjected to thorough testing with regard to functional aspects and resulting coating quality. Towards design and development of such an advanced DSC system, major challenges such as modification of existing mixing chamber, elimination of numerous mechanically moving parts such as cam, gear, piston, roller, bearings, re-engineering of solenoid valves, flashback arresters, mass flow controller, PLC computer controlled system have been successfully accomplished. Subsequent to the integration of all newly designed and re-engineered parts with the main assembly system, numerous coatings were generated at higher detonation frequencies such as 6Hz, process parameters were optimized to achieve the bench mark coating quality. The new system with enhanced functional features and increased productivity and reliability will be transferred to the existing technology receivers and also to the other industries.
Key Features
- High productivity due to high pulse frequency
- Less maintenance: absence of mechanically moving parts
- Good adhesion strength (>10000 psi)
- Dense microstructure (< 1%)
- Negligible thermal degradation and excellent tribological properties
- Ability to coat wide range of powders, carbide, oxide, metal powders
- Lower substrate temperature & low oxide content
- Coatings with 50-2000 microns thickness can be produced
Potential Applications
- Steel industry application such as Bridle rolls
- Textile & Paper industry applications such as wire passing pulleys, plungers, steeped cone pulleys, bearing stopper plates, guide rolls
- Gas compressor applications such as spindle valve, compressor disc, compressor shaft
- Strategic applications like HP & LP turbine blades, compressor discs, LCA nozzles, thrust beating sleeves, propeller shaft seals.
- Power and Energy applications such as guide vanes, spindle valves, hydro turbine blades.
Intellectual Property Development Indices (IPDI) 
- Process parameters were optimized, coating quality, repeatability and reliability studies were completed
- Subsequent to the technology launch, new systems will be fabricated, inspected, tested and transferred to the interested industries
Status | 1 | 2 | 3 | 4 | 5 | 6 | 7 | 8 | 9 | 10 |
Major Patents / Publications
Major Publications
- D. Srinivasa Rao et al, Detonation Sprayed Coatings for Aerospace Applications, in “Aerospace Materials and Material Technologies”, Ed: N.E. Prasad, R.J.H. Wanhill, Pubs: Indian Institute of Metals Series, Springer Science + Business Media, Singapore, 2017, pp: 483-500, ISBN: 978-981-10-2143-5, Article DOI: 10.1007/978-981-10-2134-3_22.
- D.Srinivasa Rao et al, “Detonation Sprayed Coatings and Their Tribological Performance” in Thermal Sprayed Coatings and Their Tribological, M. Roy, & J. Davim (Eds.) Thermal Sprayed Coatings and their Tribological Performances, IGI Global, 2015. (pp. 294-327). Hershey, PA: Engineering Science Reference. doi:10.4018/978-1-4666-7489-9.ch010
High Pressure Cold Spray Technology
Overview
Cold gas dynamic spray (also called Cold Spray or Kinetic Spray) involves accelerating micron sized powder particles to supersonic velocities resulting in the formation of dense, thick and pure coatings with high deposiotion rates. Cold spray is a low temperature high velocity variant of thermal spray family. This technique has very high deposition rates and deposition efficiencies. Since there is no heating of powders, retention of powder properties in the coating is possible. Dense coatings with porosity less than 0.1% can be achieved. Metallic, Alloy, Composites, Nanostructured and Amorphous powders can be deposited. This technology has huge potential for repair and refurbishment, electrical and thermal applications. The uniqueness is to target dense coatings that need very high particle velocities to get deposited using cold spray and to deposit dense coatings of Refractory Metals, Molybdenum, Cobalt based materials, superalloys, metal-metal carbide composites without having to resort for a post treatment procedure.
Key Features
- Indigenously developed state of the art PLC based automated Portable control panel (Max Pressure – 100 bar)
- High Mach Number Nozzles (>3)
- Maximum Pressure-50 bar; Maximum Temperature-600oC
- Steels, Super Alloys, Molybdenum, HEAs, Refractory coatings
- Indigenously designed and fabricated High Pressure Heater
- Indigenously designed and fabricated High Pressure Gun and Powder Feeder
- Indigenously desined and fabricated high mach number nozzles
Potential Applications
- Repair and Refurbishment Applications
- Coatings for Electrical contacts, lugs, EMI shielding, heat sinks
- Coatings for High Temp Corrosion resistance, Bio medical, Sputter Target
- Super Alloy coatings for high temperature wear and corrosion applications
- Wear resistant coatings (Metal-Metal Carbides)
- Nanostrcutured / amorpohous/ BMG coatings
- High Entropy Alloy Coatings for Bondcoats for High Temperature Gas Turbine Apploications Applications
Intellectual Property Development Indices (IPDI) 
- Preliminary Process Development Level
Status | 1 | 2 | 3 | 4 | 5 | 6 | 7 | 8 | 9 | 10 |
Major Patents / Publications
Major Publications
- Naveen M Chavan, SP Phani, M Ramakrishna, DS Rao and G Sundararajan, Surface & Coatings Technology 205 (2011), P4798–4807
- G Sundararajan, Naveen M Chavan and S Kumar, Journal of Thermal Spray Technology, 1348—Volume 22(8) December 2013
- S Kumar, A.Jyothirmayi, Nitin Wasekar and SV Joshi, Surface and Coatings Technology, 296(2016), 124-135
Detonation Spray Coating Technology (DSC)
Overview
DSC is a thermal spray process capable of producing coatings with extremely good adhesive strength, and low porosity with compressive residual stresses. Metered proportion of the combustion mixture comprising of oxygen and acetylene (oxy-fuel: OF ratio) is fed through a tubular barrel closed at one end. The gas mixture inside the chamber is ignited by a simple spark plug and the combustion generates high pressure shock waves (detonation wave), which then propagate through the gas stream. Simultaneous admission of the coating powder fed into the combustion chamber results in particle acceleration while the temperature of the hot gas stream can go up to 4000 deg C depending on the OF ratio employed. The hot gases generated in the detonation chamber while travelling down the barrel at a high velocity rapidly heats the particles to a plasticizing stage (skin melting) and also accelerate the particles to a velocity of 800-1200m/sec. These particles then come out of the barrel and impact the component surface to form the coating. The high kinetic energy of the semi-molten powder particles upon impact with the substrate result in formation of a very dense coating. The chamber is finally flushed with nitrogen to clean the barrel for subsequent detonation cycle to obtain thicker coatings. Depending on the required coating thickness and the type of coating material, the detonation spraying cycle can be repeated at the rate of 3 shots per second.
Key Features
- Good adhesion strength (>10000 psi)
- Dense microstructure (< 1%)
- Negligible thermal degradation
- Good surface finish (~4-6 mm Ra)
- Ability to coat wide range of powders
- Lower substrate temperature & low oxide content
- Good tribological properties
- Coatings with 50-2000 microns thickness can be produced
Potential Applications
- Steel industry application such as Bridle rolls
- Textile & Paper industry applications such as wire passing pulleys, plungers, steeped cone pulleys, bearing stopper plates, guide rolls
- Gas compressor applications such as spindle valve, compressor disc, compressor shaft
- Strategic applications like HP & LP turbine blades, compressor discs, LCA nozzles, thrust beating sleeves, propeller shaft seals.
- Power and Energy applications such as guide vanes, spindle valves, hydro turbine blades.
Intellectual Property Development Indices (IPDI) 
- Multiple number of prototype industry scale systems were thoroughly tested and transferred to technology receivers across the country
- Coating production using DSC is fully streamlined (Arial Narrow 10 pt – Not more than 3 bullet points of one line)
Status | 1 | 2 | 3 | 4 | 5 | 6 | 7 | 8 | 9 | 10 |
Major Patents / Publications
Major Publications
- D. Srinivasa Rao et al, Detonation Sprayed Coatings for Aerospace Applications, in “Aerospace Materials and Material Technologies”, Ed: N.E. Prasad, R.J.H. Wanhill, Pubs: Indian Institute of Metals Series, Springer Science + Business Media, Singapore, 2017, pp: 483-500, ISBN: 978-981-10-2143-5, Article DOI: 10.1007/978-981-10-2134-3_22.
- D.Srinivasa Rao et al, “Detonation Sprayed Coatings and Their Tribological Performance” in Thermal Sprayed Coatings and Their Tribological, M. Roy, & J. Davim (Eds.) Thermal Sprayed Coatings and their Tribological Performances, IGI Global, 2015. (pp. 294-327). Hershey, PA: Engineering Science Reference. doi:10.4018/978-1-4666-7489-9.ch010
Electron Beam Physical Vapour Deposition System (EBPVD)
Overview
EBPVD technology is known to deposit the coatings with columnar microstructure which results in enhanced strain tolerance and erosion resistant at high temperatures. Owing to this specific technological feature, EBPVD coatings are popularly employed for depositing the ceramic coatings with extremely lower thermal conductivity. One of the best known configurations of such thermal barrier coating (TBC) is the top coat of yttria stabilized zirconia (YSZ) with a suitable bond coat on aero engine gas turbine blades and vanes. Further, EBPVD technology is also suitable for depositing a wide variety of metallic, alloy and composite materials which is also suitable for the bond coat applications such as MCrAlY (M = Ni or Co) on the super alloy substrates for enhanced functional performance. Such an EBPVD technological unit with specific features and special capabilities has been established at ARCI in collaboration with M/s International centre for Electron beam technologies, Kiev, Ukraine for readily serving the Indian industry. The EBPVD consisting of multiple EB guns which will melt and evaporate the ingot materials under specific vacuum conditions in a controlled chamber wherein the vaporised materials get subsequently deposited on the substrate materials. Specialized jigs and fixtures were designed and processing parameters were optimized to provide the TBC’s on a variety of components needing protection against the high temperatures. In addition, an innovative methodology has been created to benefit the Indian strategic sector and industry for refurbishing and repairing a variety of blades and vanes indigenously during engine’s periodic overhauls thus saving notable amount of foreign currency.
Key Features
- Coatings obtained are dense, uniform and smooth
- Possible to obtain gradient compositions, structure and properties as required
- 50-100 µm/hr deposition rate with a productivity of 10-15 kg/hr
- Large window of coating thickness (10μm-2 mm)
- Ability to coat thin foils, strips, sheets & heavy blanks
Potential Applications
- By changing the processing conditions such as ingot composition, part manipulation and EB energy, EB-PVD technology is capable of depositing various coatings such as: functional gradient coatings, multilayered thick ceramic coatings, textured multilayer coatings, biological coatings
- Hot Corrosion & Oxidation Resistant Coatings
- Uniform Thermal Barrier Coatings (TBCs)
- Damping and Wear Resistant Coatings
- Thick Repair Coatings up to 1-2 mm
Intellectual Property Development Indices (IPDI) 
- Application development in aero engine and power sector turbine blade and sponsored project on development of TBC coating rotor HP rotor turbine blades for helicopter engine is currently in progress at ARCI.
Status | 1 | 2 | 3 | 4 | 5 | 6 | 7 | 8 | 9 | 10 |
Major Patents / Publications
Major Patents
Major Publications
- D. Srinivasa Rao et al, Processing-Structure-Property Relationships in EB-PVD Yttria Stabilized Zirconia (YSZ) Coatings, Journal of Vacuum Science & Technology A 29, 2011
- Dipak K. Das, D.Srinivasa Rao et al, Singh, Microstructure, Texture and Thermal Cycling Performance of EB-PVD TBCs Deposited under Different Processing Conditions, Journal of High Temperature Materials and Processes, Vol.30(2011),pp.539-548